Steel burning method with forward thermal load
A technology of heat load and heating temperature, which is applied in the field of steel burning with advance heat load, and slab steel burning for hot-rolled plate production. Even temperature effect
- Summary
- Abstract
- Description
- Claims
- Application Information
AI Technical Summary
Problems solved by technology
Method used
Image
Examples
Embodiment 1
[0017] Embodiment 1: The present invention proposes a steel burning method with a heat load shifted forward. The method is aimed at the actual situation that the heating curves of slabs are greatly different and cannot be unified. Fluctuation is used to realize the process stability and consistency in the second half of the heating process (two-addition, soaking section) as much as possible, and realize the second-addition section and soaking section. Compared with the conventional steel firing, which only requires the end temperature of the second heating section and the end slab of the soaking section (the target temperature of the slab coming out of the furnace), the temperature requirement at the end of the first heating section is added. Conventional soaking requires a gentle temperature rise, and the present invention also requires a gentle temperature rise as much as possible to reduce the temperature rise level, ensure that the slab is thoroughly burned, and improve the...
PUM
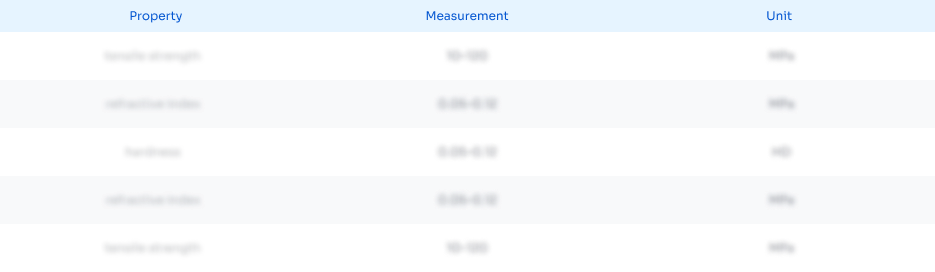
Abstract
Description
Claims
Application Information

- R&D Engineer
- R&D Manager
- IP Professional
- Industry Leading Data Capabilities
- Powerful AI technology
- Patent DNA Extraction
Browse by: Latest US Patents, China's latest patents, Technical Efficacy Thesaurus, Application Domain, Technology Topic, Popular Technical Reports.
© 2024 PatSnap. All rights reserved.Legal|Privacy policy|Modern Slavery Act Transparency Statement|Sitemap|About US| Contact US: help@patsnap.com