Fiber preform forming method of ceramic matrix composite longitudinal corrugated heat insulation screen
A corrugated heat shield and composite material technology, applied in combustion methods, chemical instruments and methods, lighting and heating equipment, etc., can solve the problems of difficulty in forming fiber preforms, low mold attachment rate, etc. The effect of reducing production cost and reducing fiber damage
- Summary
- Abstract
- Description
- Claims
- Application Information
AI Technical Summary
Problems solved by technology
Method used
Image
Examples
Embodiment 1
[0037] A method for forming a fiber prefabricated body of a ceramic matrix composite material longitudinal corrugated heat shield, comprising the following steps:
[0038] (1) adopt high-purity graphite, take the inner and outer profiles of the heat shield as a reference, prepare the inner mold 1 and the outer mold of the shaping mold respectively; wherein, the inner mold 1 and the outer mold have a number of diameters perpendicular to the mold surface. The air hole is 5mm, the axial height of the shaping die is 1.12 times the height of the heat shield member, the wall thickness of the shaping die is 10mm, the inner mold 1 and the outer mold of the shaping mold are 6 sectors distributed along the circumferential direction of the heat shield Combination of segment parts;
[0039] (2) Wrap the two-dimensionally woven carbon fiber plain cloth on the inner mold 1, and use polyvinyl alcohol environmental protection glue to complete the bonding of the two-dimensionally woven carbon ...
Embodiment 2
[0045] A method for forming a fiber prefabricated body of a ceramic matrix composite material longitudinal corrugated heat shield, comprising the following steps:
[0046] (1) Using electrode graphite, with the inner and outer profiles of the heat shield as a reference, prepare the inner mold 1 and the outer mold of the shaping mold respectively; wherein, the inner mold 1 and the outer mold have a number of diameters perpendicular to the mold surface of 3mm The axial height of the shaping die is 1.1 times the height of the heat shield components, the wall thickness of the shaping die is 5mm, and the inner mold 1 and the outer mold of the shaping die are 6 fan-shaped segments distributed along the circumferential direction of the heat shield combination of parts;
[0047] (2) Wrap the two-dimensionally woven carbon fiber plain cloth on the inner mold 1, and use polyvinyl alcohol environmental protection glue to complete the bonding of the two-dimensionally woven carbon fiber pl...
Embodiment 3
[0053] A method for forming a fiber prefabricated body of a ceramic matrix composite material longitudinal corrugated heat shield, comprising the following steps:
[0054] (1) adopt high-purity graphite, take the inner and outer profiles of the heat shield as a reference, prepare the inner mold 1 and the outer mold of the shaping mold respectively; wherein, the inner mold 1 and the outer mold have a number of diameters perpendicular to the mold surface. The air hole is 10mm, the axial height of the shaping die is 1.5 times the height of the heat shield member, the wall thickness of the shaping die is 15mm, and the inner mold 1 and the outer mold of the shaping die are 6 sectors distributed along the circumferential direction of the heat shield Combination of segment parts;
[0055] (2) Wrap the two-dimensionally woven carbon fiber plain cloth on the inner mold 1, and use polyvinyl alcohol environmental protection glue to complete the bonding of the two-dimensionally woven carb...
PUM
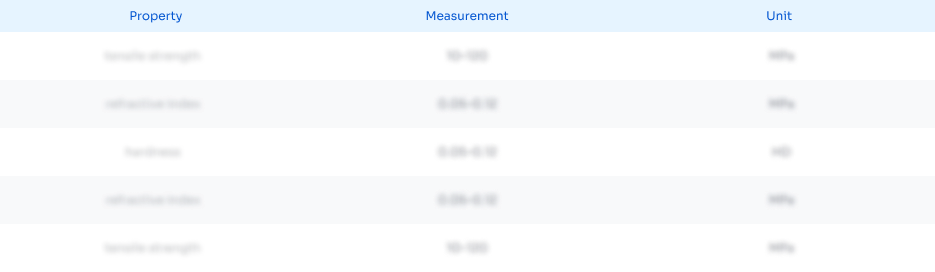
Abstract
Description
Claims
Application Information

- R&D
- Intellectual Property
- Life Sciences
- Materials
- Tech Scout
- Unparalleled Data Quality
- Higher Quality Content
- 60% Fewer Hallucinations
Browse by: Latest US Patents, China's latest patents, Technical Efficacy Thesaurus, Application Domain, Technology Topic, Popular Technical Reports.
© 2025 PatSnap. All rights reserved.Legal|Privacy policy|Modern Slavery Act Transparency Statement|Sitemap|About US| Contact US: help@patsnap.com