Strip head shearing and butt welding method and shearing and butt welding platform
A butt welding and platform technology, applied in other manufacturing equipment/tools, manufacturing tools, etc., can solve the problems of high raw material cost, large raw material, waste, etc., and achieve the effects of improving production efficiency, rational use, and saving raw materials
- Summary
- Abstract
- Description
- Claims
- Application Information
AI Technical Summary
Problems solved by technology
Method used
Image
Examples
Embodiment 1
[0033] Such as figure 1 , figure 2 As shown, it is the shear butt welding platform of the present invention, its base 1 is a cuboid frame platform, the long frame is located at the front and rear sides, the short frame is located at the left and right sides, the rear end of the base 1 is the input end of the steel strip 20, and the front end is the The output end of the steel belt 20, the steel belt 20 is conveyed forward with the direction perpendicular to the central axis 23 of the short frame; as figure 1 As shown, a bracket 8 is provided above the base 1 at a certain distance from the top surface of the base 1, and a screw 9 is arranged on the bracket 8, and the screw 9 is connected with the driving device (not shown in the figure), and the screw 9 is connected There are several second slide blocks 16, the second slide block 16 is fixedly connected with the slide block 10, and the screw mandrel 9 drives the slide block 10 to move left and right by the second slide block ...
Embodiment 2
[0038] Such as image 3 As shown, according to the actual installation space of the production workshop, the shearing butt welding platform according to the present invention can also arrange the milling and flattening station separately, instead of being set on the same base 1 together with the shearing station and the welding station The front and rear sides of the base 1 are provided with a supporting device 19, the base 1 is provided with a cutting station and a welding station, the upper cutter 7 and the welding torch 12 are set on the slide 10, and the outer side of the supporting device 19 at the output end of the base 1 is set Milling machine 24, the milling cutter 13 and the third groove 15 are set on the milling machine 24, and after the strip head of the steel strip 20 rolled forward and backward is cut and welded on the base 1, it is transported to the milling machine 24 by the supporting device 19 for welding. 22 milling to complete the whole process.
[0039] In...
PUM
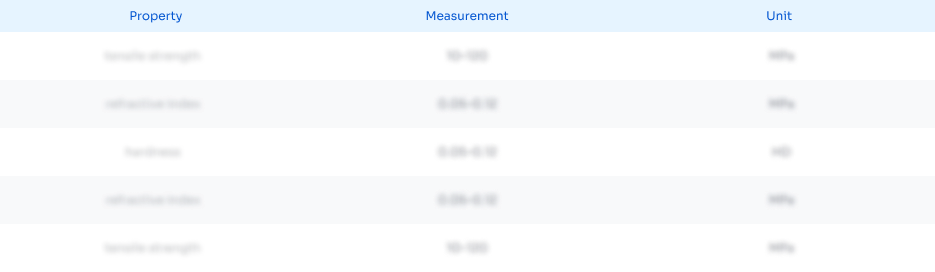
Abstract
Description
Claims
Application Information

- R&D
- Intellectual Property
- Life Sciences
- Materials
- Tech Scout
- Unparalleled Data Quality
- Higher Quality Content
- 60% Fewer Hallucinations
Browse by: Latest US Patents, China's latest patents, Technical Efficacy Thesaurus, Application Domain, Technology Topic, Popular Technical Reports.
© 2025 PatSnap. All rights reserved.Legal|Privacy policy|Modern Slavery Act Transparency Statement|Sitemap|About US| Contact US: help@patsnap.com