Mold and method for manufacturing special-shaped composite material rotary body by using mold
A composite material and rotary body technology, which is applied in the field of special-shaped variable-section thin-walled rotary body production, can solve the problems of inability to produce special-shaped and variable-section products, low lateral strength of pultrusion process, low longitudinal strength of winding process, etc., to save investment. and maintenance cost, increase the winding process, the effect of simple surface treatment process
- Summary
- Abstract
- Description
- Claims
- Application Information
AI Technical Summary
Problems solved by technology
Method used
Image
Examples
Embodiment Construction
[0033] In order to make the purpose, technical solutions and advantages of the embodiments of the present invention more clear, the following will be combined with the appended Figure 1-3 , clearly and completely describe the technical solutions of the embodiments of the present invention. Apparently, the described embodiments are some, not all, embodiments of the present invention. All other embodiments obtained by those skilled in the art based on the described embodiments of the present invention belong to the protection scope of the present invention.
[0034] Such as Figure 1-3 Shown: the present invention provides a kind of mould, comprises rotary external mold a6, rotary external mold b8, described rotary external mold a6 and rotary external mold b8 are detachably connected, described rotary external mold a6, rotary external mold b8 are connected A rotary inner mold 1 is arranged in the cavity formed afterward, and gaps are formed between the inner walls of the rota...
PUM
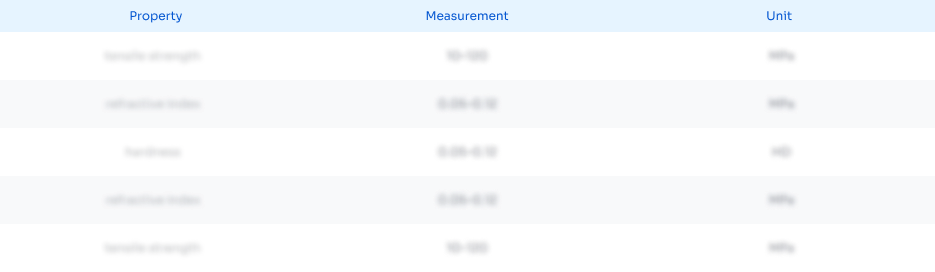
Abstract
Description
Claims
Application Information

- Generate Ideas
- Intellectual Property
- Life Sciences
- Materials
- Tech Scout
- Unparalleled Data Quality
- Higher Quality Content
- 60% Fewer Hallucinations
Browse by: Latest US Patents, China's latest patents, Technical Efficacy Thesaurus, Application Domain, Technology Topic, Popular Technical Reports.
© 2025 PatSnap. All rights reserved.Legal|Privacy policy|Modern Slavery Act Transparency Statement|Sitemap|About US| Contact US: help@patsnap.com