Temperature control method for rolled strip steel in ferrite area
A temperature control method and ferrite technology, applied in the direction of temperature control, metal rolling, etc., can solve the problems of difficult to arrange cooling equipment, long time for air cooling, long cooling swing time, etc. Effect of rolling pressure, improving strip structure and mechanical properties
- Summary
- Abstract
- Description
- Claims
- Application Information
AI Technical Summary
Problems solved by technology
Method used
Image
Examples
Embodiment 1
[0026] like figure 1 As shown, the embodiment is selected for the IF steel (ultra-low carbon) slab, the ferritic region rolling, the slab component is: c ≤ 0.01%, Si ≤ 0.03%, Mn ≤ 0.2%, P ≤ 0.02 by weight percent. %, S ≤ 0.015%, Al ≤ 0.06%, N ≤ 0.004%, Ti ≤ 0.12%, margin is Fe. In the cooling rate of 1 to 3 ° C / s, its ferrite phase change termination temperature AC 3f 860 ° C, Austenite AC 3 The temperature is 910 ° C; the annealing re-crystallization temperature after cold rolling is over 660 ° C. The stable rolling speed of the thick roller is 5.5m / s, the rough rolling mill is 1.3m / s, and the roll line speed of the front rough rolling mill is 1m / s. 2 .
[0027] In this embodiment, a hot roller box 5 is provided between the thick rolling mill 3 and the finishing mill portion of the hot rolling production line, and the first intermediate blank cooling device 4-1 is provided at the outlet of the thick rolling mill, at the exit of the hot cabinet 5. Set the second intermedia...
Embodiment 2
[0038] In this example, the 08Al low carbon steel slab is used for ferritic region rolling test. The slab component is: c ≤ 0.08%, Mn ≤ 0.40%, P ≤ 0.025%, s ≤ 0.02%, Al ≤ 0.04% by weight percent. The margin is Fe. At a cooling rate of 1 to 3 ° C / s, the phase change temperature AR3F is 820 ° C, the austenite AC3 temperature is 880 ° C, and the annealing re-crystallization temperature of 620 ° C after cold rolling.
[0039] like figure 2 As shown, the present embodiment replaces the thermal cabinet of the first embodiment to the insulation cover 6 to reduce the tail temperature difference of the blank blank. The stable rolling speed of the thick rolling mill is 5.5m / s, the end of the rough rolling mill is 1 m / s, the roll line speed of the front rough mill of the polishing machine is 1m / s 2 .
[0040] The temperature control method of rolling strip steel in the ferrite region of the present embodiment includes the following steps:
[0041] like figure 2 As shown, the first, s...
PUM
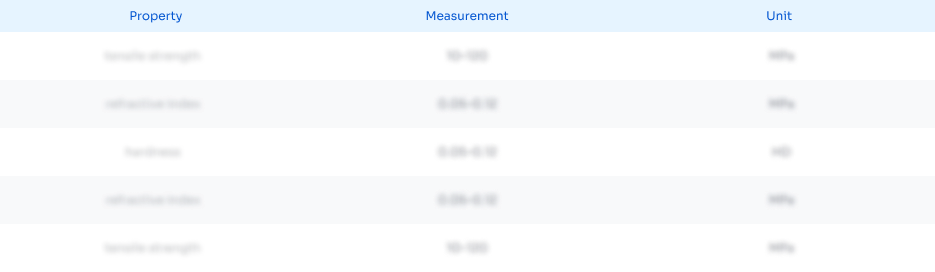
Abstract
Description
Claims
Application Information

- R&D
- Intellectual Property
- Life Sciences
- Materials
- Tech Scout
- Unparalleled Data Quality
- Higher Quality Content
- 60% Fewer Hallucinations
Browse by: Latest US Patents, China's latest patents, Technical Efficacy Thesaurus, Application Domain, Technology Topic, Popular Technical Reports.
© 2025 PatSnap. All rights reserved.Legal|Privacy policy|Modern Slavery Act Transparency Statement|Sitemap|About US| Contact US: help@patsnap.com