A method for separating beryllium from beryllium-containing sludge based on mineral phase reconstruction
A sludge and mineral phase technology, applied in sludge treatment, chemical instruments and methods, water/sludge/sewage treatment, etc., can solve the problems of failure to detoxify beryllium-containing waste and re-release of beryllium, and achieve Low processing cost, mild reaction conditions, and the effect of reducing beryllium pollution
- Summary
- Abstract
- Description
- Claims
- Application Information
AI Technical Summary
Problems solved by technology
Method used
Image
Examples
Embodiment 1
[0060] Sampling and analysis of beryllium-containing sludge:
[0061] The beryllium-containing sludge after drying and dehydration in a factory was taken, and the solid samples were digested with nitric acid and hydrochloric acid. The sludge mainly contains elements such as Ca, Si, O, S, among which Ca mainly exists in the form of calcium sulfate, and Si mainly exists in the form of silica.
[0062] The SEM-EDS image of the sample was measured (see figure 2 ), based on the image, it can be concluded that calcium sulfate and silica are two phases in the solid phase, wherein calcium sulfate is gypsum crystal, and silica is an amorphous flocculent aggregate. The XRD pattern of the sample was obtained again (see image 3 ), only the peak of calcium sulfate exists in the figure, and there is no peak of silica. Based on the two figures, it can be concluded that the silica in the solid phase is amorphous. Elemental distribution map of the electron probe of the sample (see Figu...
Embodiment 2
[0064]Put 1 kilogram of the beryllium-containing sludge sample described in Example 1 into a ball mill for wet ball milling pretreatment. After grinding to 400 mesh, it is fully mixed and stirred with 10 liters of 0.5 mol / L sulfuric acid to obtain a solid-liquid mixture. The liquid mixture was put into a hydrothermal kettle, and the hydrothermal kettle was sealed, heated to 120 ° C, and reacted for 4 hours. After the reaction was completed, it was allowed to stand and cool to room temperature. The hydrothermal kettle is opened, and the solid-liquid mixture is separated by means of filtration, centrifugation, etc., to obtain a beryllium-containing filtrate and a beryllium-depleted filter residue. The beryllium-containing filtrate is returned to the beryllium smelting process, and the filter residue is washed with water, filtered / centrifuged 3 times, and detoxified waste residue is obtained. The beryllium content in the beryllium-containing filtrate was measured, and the berylli...
Embodiment 3
[0080] The described beryllium-containing sludge sample in 1 kilogram of embodiment 1 is put into a ball mill for wet ball milling pretreatment, and after grinding to 300 meshes, mixed with 5 liters of sulfuric acid and hydrochloric acid (total concentration 1mol / L, v sulfuric acid: v hydrochloric acid=1:1) After fully mixing and stirring, the solid-liquid mixture was put into a hydrothermal kettle, and the hydrothermal kettle was sealed, heated to 180 ° C, and reacted for 3 hours. The hydrothermal kettle is opened, and the solid-liquid mixture is separated by means of filtration, centrifugation, etc., to obtain a beryllium-containing filtrate and a beryllium-depleted filter residue. The beryllium-containing filtrate is returned to the beryllium smelting process, and the filter residue is washed with water, filtered / centrifuged for 5 times, and detoxified waste residue is obtained. The beryllium content in the beryllium-containing filtrate was measured, and the beryllium conte...
PUM
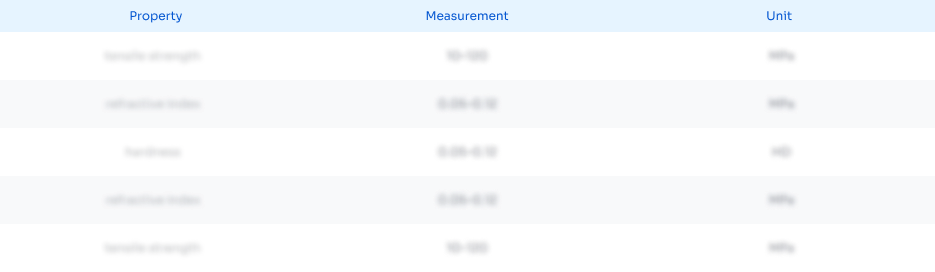
Abstract
Description
Claims
Application Information

- R&D
- Intellectual Property
- Life Sciences
- Materials
- Tech Scout
- Unparalleled Data Quality
- Higher Quality Content
- 60% Fewer Hallucinations
Browse by: Latest US Patents, China's latest patents, Technical Efficacy Thesaurus, Application Domain, Technology Topic, Popular Technical Reports.
© 2025 PatSnap. All rights reserved.Legal|Privacy policy|Modern Slavery Act Transparency Statement|Sitemap|About US| Contact US: help@patsnap.com