Strain clamp crimping process optimization method and device based on finite element simulation
A tension clamp, process optimization technology, applied in design optimization/simulation, special data processing applications, instruments, etc., can solve the problems of large residual stress of tension clamp and lack of targeted optimization, and achieve residual stress optimization, Reduce the possibility of fracture failure, highly targeted effect
- Summary
- Abstract
- Description
- Claims
- Application Information
AI Technical Summary
Problems solved by technology
Method used
Image
Examples
Embodiment
[0051] In the power transmission system, the strain clamp is very important. However, the plastic deformation of the existing strain clamp during the crimping process of the aluminum tube and the steel anchor is easy to generate residual stress, which brings safety hazards to the operation of the power system. Therefore, this embodiment provides a method for optimizing the crimping process of strain clamps based on finite element simulation. This embodiment obtains the distribution of residual stress by modeling and simulating the strain clamps, and performs the process by improving the mold model. optimization.
[0052] Specific as figure 1 As shown, the method of the present embodiment includes the following steps:
[0053] In step 101, the measured parameters of each component of the tension clamp and the crimping die are obtained.
[0054] This embodiment takes figure 2 The original tension clamp structure shown is an example, which includes aluminum tube 1, aluminum s...
Embodiment 2
[0077] This embodiment proposes a strain clamp crimping process optimization device based on finite element simulation, specifically as Figure 8 As shown, the device of this embodiment includes a parameter acquisition unit, a modeling unit, a simulation unit and an optimization unit.
[0078] Among them, the parameter acquisition unit is used to obtain the measured parameters of the various components of the tension clamp and the crimping die, including the measured size parameters of each component and the crimping position parameters, etc., and determine the material of each component, so as to determine Including yield strength, Young's modulus, Poisson's ratio, material density and other mechanical parameters.
[0079] The modeling unit constructs models of the components of the tension clamp and the crimping die according to the measured parameters of the components of the strain clamp and the crimping die. The modeling process specifically includes geometric model estab...
PUM
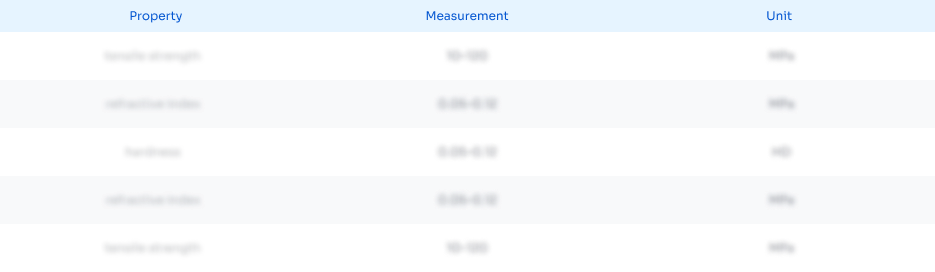
Abstract
Description
Claims
Application Information

- R&D
- Intellectual Property
- Life Sciences
- Materials
- Tech Scout
- Unparalleled Data Quality
- Higher Quality Content
- 60% Fewer Hallucinations
Browse by: Latest US Patents, China's latest patents, Technical Efficacy Thesaurus, Application Domain, Technology Topic, Popular Technical Reports.
© 2025 PatSnap. All rights reserved.Legal|Privacy policy|Modern Slavery Act Transparency Statement|Sitemap|About US| Contact US: help@patsnap.com