Variable-stiffness damping supporting mechanism for reusable rocket
A supporting mechanism and variable stiffness technology, applied in the direction of projectiles, self-propelled bombs, offensive equipment, etc., can solve the problems of complex manufacturing process, structural plastic deformation, low pass rate, etc., to achieve safety protection, reduce vibration level, Effect of Ensuring Separation Margin
- Summary
- Abstract
- Description
- Claims
- Application Information
AI Technical Summary
Problems solved by technology
Method used
Image
Examples
Embodiment Construction
[0041] The present invention will be further elaborated below in conjunction with embodiment.
[0042] A variable stiffness damping support mechanism for reusable rockets, including a swing arm assembly 1, a support rod assembly 2, a telescopic curved beam assembly 3, and a mount assembly 4. The contracted state is as follows: figure 1 As shown, the expanded state is as follows figure 2 shown. In the retracted state, the swing arm, support rod and telescopic curved beam assembly are all in close contact with the shell segment of the cylindrical shell or the inner surface of the fairing, reducing the space occupied by the rocket. When it needs to be unfolded, the external constraints are in contact, and the swing arm components on both sides are rotated and expanded under the action of the driving source, which drives the telescopic curved beam in the middle to shrink and rise, and at the same time drives the support rod to extend and rotate to rise. When the mechanism is un...
PUM
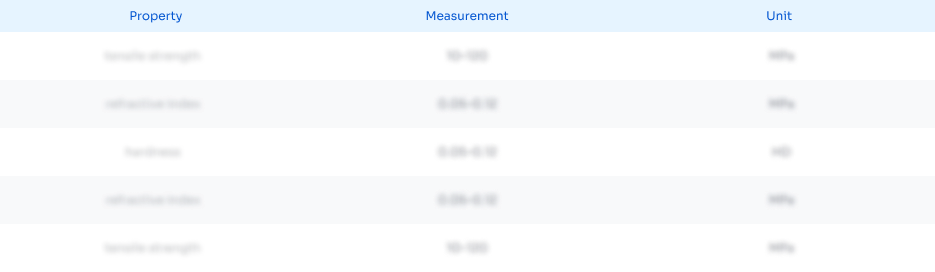
Abstract
Description
Claims
Application Information

- Generate Ideas
- Intellectual Property
- Life Sciences
- Materials
- Tech Scout
- Unparalleled Data Quality
- Higher Quality Content
- 60% Fewer Hallucinations
Browse by: Latest US Patents, China's latest patents, Technical Efficacy Thesaurus, Application Domain, Technology Topic, Popular Technical Reports.
© 2025 PatSnap. All rights reserved.Legal|Privacy policy|Modern Slavery Act Transparency Statement|Sitemap|About US| Contact US: help@patsnap.com