Preparation method of yttrium oxide dispersion strengthened copper alloy
A technology for dispersion strengthening copper and yttrium trioxide, applied in the field of strengthening copper alloys, can solve the problems of many influencing factors, insufficient room temperature plasticity, long cycle, etc. strong effect
- Summary
- Abstract
- Description
- Claims
- Application Information
AI Technical Summary
Problems solved by technology
Method used
Examples
Embodiment 1
[0025] The invention provides a technical solution: a method for preparing a diyttrium trioxide dispersion-strengthened copper alloy, comprising the following steps:
[0026] Step 1: using Cu (99.99%) and Y (99.9%) metal raw materials to prepare a Cu-Y alloy by weight percentage, the weight percentage of Cu is 35%, and the weight percentage of Y is 65%;
[0027] Step 2: Mix the weighed metal raw materials in the water-cooled copper crucible of the non-consumable arc melting furnace, and melt the alloy ingot under the protection of the protective gas. The working current of the arc melting in the non-consumable arc melting furnace is 60A;
[0028] Step 3: Put the alloy ingot into the quartz tube after crushing, and prepare Cu-Y amorphous by using vacuum copper roller single-roller spin quenching technology. The crushed alloy ingot needs to be screened through a 100-mesh sieve before being put into the quartz tube;
[0029] Step 4: Crush the Cu-Y amorphous alloy ingot and put i...
Embodiment 2
[0036] The invention provides a technical solution: a method for preparing a diyttrium trioxide dispersion-strengthened copper alloy, comprising the following steps:
[0037] Step 1: using Cu (99.99%) and Y (99.9%) metal raw materials to prepare a Cu-Y alloy by weight percentage, the weight percentage of Cu is 55%, and the weight percentage of Y is 45%;
[0038] Step 2: Mix the weighed metal raw materials in the water-cooled copper crucible of the non-consumable arc melting furnace, and melt the alloy ingot under the protection of the protective gas. The working current of the arc melting in the non-consumable arc melting furnace is 100A;
[0039] Step 3: Put the alloy ingot into the quartz tube after crushing, and prepare Cu-Y amorphous by using vacuum copper roller single-roller spin quenching technology. The crushed alloy ingot needs to be screened through a 100-mesh sieve before being put into the quartz tube;
[0040] Step 4: Crush the Cu-Y amorphous alloy ingot and put ...
Embodiment 3
[0047] The invention provides a technical solution: a method for preparing a diyttrium trioxide dispersion-strengthened copper alloy, comprising the following steps:
[0048] Step 1: using Cu (99.99%) and Y (99.9%) metal raw materials to prepare a Cu-Y alloy by weight percentage, the weight percentage of Cu is 60%, and the weight percentage of Y is 40%;
[0049] Step 2: Mix the weighed metal raw materials in the water-cooled copper crucible of the non-consumable arc melting furnace, and melt the alloy ingot under the protection of the protective gas. The working current of the arc melting in the non-consumable arc melting furnace is 150A;
[0050] Step 3: Put the alloy ingot into the quartz tube after crushing, and prepare Cu-Y amorphous by using vacuum copper roller single-roller spin quenching technology. The crushed alloy ingot needs to be screened through a 100-mesh sieve before being put into the quartz tube;
[0051] Step 4: Crush the Cu-Y amorphous alloy ingot and put it...
PUM
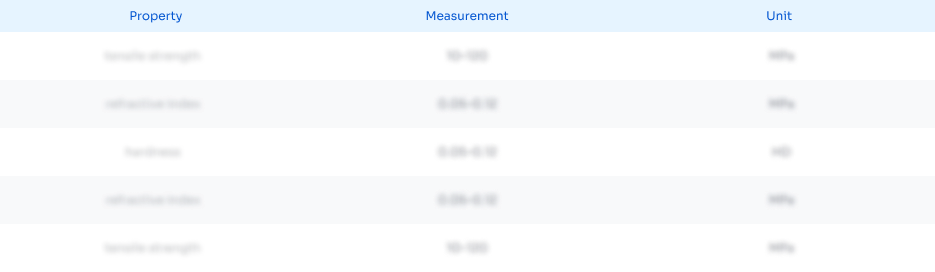
Abstract
Description
Claims
Application Information

- R&D Engineer
- R&D Manager
- IP Professional
- Industry Leading Data Capabilities
- Powerful AI technology
- Patent DNA Extraction
Browse by: Latest US Patents, China's latest patents, Technical Efficacy Thesaurus, Application Domain, Technology Topic, Popular Technical Reports.
© 2024 PatSnap. All rights reserved.Legal|Privacy policy|Modern Slavery Act Transparency Statement|Sitemap|About US| Contact US: help@patsnap.com