Thermoplastic plastic hot-press forming mold and mold taking method thereof
A thermoplastic, hot-pressing molding technology, applied in sampling, analyzing materials, measuring devices, etc., can solve problems such as difficulty and single mold taking, and achieve the effect of simple operation, solving difficult mold taking, and not easy to damage.
- Summary
- Abstract
- Description
- Claims
- Application Information
AI Technical Summary
Problems solved by technology
Method used
Image
Examples
specific Embodiment
[0040] Specific examples are as follows: Prepare ultra-high molecular weight polyethylene raw powder (ultra-high molecular weight polyethylene powder is used in this embodiment, but this molding die is applicable to all thermoplastic materials). Place the lower formwork 10 on a flat position, install the mold taking pad 9 on the lower formwork 10, fix the middle formwork 8 and the lower formwork 10 through the fixing bolts 11, and place Figure 7 For the tensile sample mold shown, add ultra-high molecular weight polyethylene powder to the inside of the mold. The thickness of the tensile sample mold should be slightly smaller than the standard thickness, so as to prevent the thickness from reaching If it is less than the standard requirement, the upper template 7 is placed to realize mold closing.
[0041] Put the installed hot pressing mold into the platform center of the hot press, start the hot press, set the temperature at 100°C-500°C, and the pressure at 2-30Mpa, wait for ...
PUM
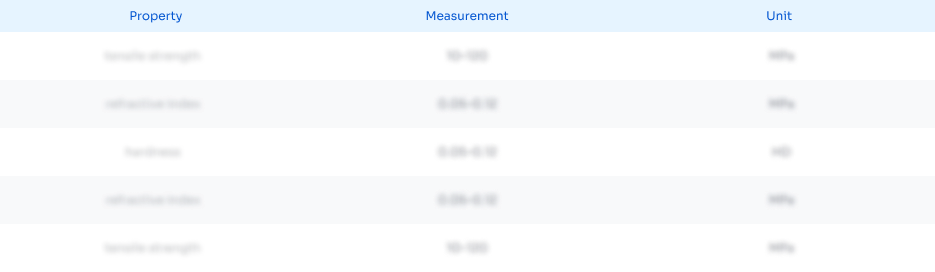
Abstract
Description
Claims
Application Information

- R&D Engineer
- R&D Manager
- IP Professional
- Industry Leading Data Capabilities
- Powerful AI technology
- Patent DNA Extraction
Browse by: Latest US Patents, China's latest patents, Technical Efficacy Thesaurus, Application Domain, Technology Topic, Popular Technical Reports.
© 2024 PatSnap. All rights reserved.Legal|Privacy policy|Modern Slavery Act Transparency Statement|Sitemap|About US| Contact US: help@patsnap.com