Process method for preparing potassium salt and byproduct magnesium salt by using corn soaking liquid
A technology of corn soaking water and process method, applied in chemical instruments and methods, alkali metal sulfite/sulfite, magnesium hydroxide, etc., can solve high-salt wastewater calcium chloride wastewater is difficult to treat, and potassium ions are effectively recovered. , environmental protection issues and other issues, to achieve the effect of increasing sustainable and stable operation, realizing zero discharge of sewage, and avoiding high-salt wastewater
- Summary
- Abstract
- Description
- Claims
- Application Information
AI Technical Summary
Problems solved by technology
Method used
Examples
Embodiment 1
[0028] (1) Get the supernatant 600L of corn soaking water after 4h subsidence, (in the supernatant, potassium ion content is 0.55%, magnesium ion content is 0.15%), enters cationic resin exchange column adsorption potassium ion with 1.5BV / h flow rate , the resin model is 001*16, and the volume is 50L; the adsorption effluent is used for the extraction and separation of other products such as phytic acid, protein, lactic acid, etc.
[0029] (2) Adsorption saturated cationic resin exchange column, after water is set to push out the residual corn soaking water, enter 1.5BV of ammonium chloride solution with ammonium ion concentration of 2mol / L to analyze the resin, after entering, enter 1.5BV of water to wash the resin column; analyze the flow rate 0.5BV / h.
[0030] (3) The analysis solution is transferred to the MVR continuous concentration crystallizer for vacuum concentration and crystallization; the concentrated crystal solution is transferred to the transfer tank, separated ...
Embodiment 2
[0033] (1) Get the supernatant 600L (0.55% of potassium ion content in the supernatant liquid, magnesium ion content is 0.15%) after 4h subsidence of corn soaking water, enter cationic resin exchange column adsorption potassium ion with 1.8BV / h flow rate, The resin model is 001*16, and the volume is 50L; the adsorption effluent is used for the extraction and separation of other products such as phytic acid, protein, lactic acid, etc.
[0034] (2) Adsorption saturated cationic resin exchange column, after water is set to push out the residual corn soaking water, enter 1.8BV of ammonium sulfate solution with ammonium ion concentration of 2mol / L to analyze the resin, and then enter 1.8BV of water to wash the resin column after entering; the analysis flow rate is 0.6 BV / h.
[0035] (3) The analysis solution is transferred to the MVR continuous concentration crystallizer for vacuum concentration and crystallization; the concentrated crystal solution is transferred to the transfer t...
Embodiment 3
[0038](1) Get the supernatant 600L (0.55% of potassium ion content in the supernatant liquid, magnesium ion content is 0.15%) after 4h subsidence of corn soaking water, enter cationic resin exchange column adsorption potassium ion with 1.6BV / h flow rate, The resin model is 001*16, and the volume is 50L; the adsorption effluent is used for the extraction and separation of other products such as phytic acid, protein, lactic acid, etc.
[0039] (2) Adsorption saturated cationic resin exchange column, after water is set to push out the residual corn soaking water, enter 1.5BV of sodium sulfate solution with a sodium ion concentration of 2mol / L to analyze the resin, and then enter 1.5BV of water to wash the resin column; the analysis flow rate is 0.8 BV / h.
[0040] (3) The analysis solution is transferred to the MVR continuous concentration crystallizer for vacuum concentration and crystallization; the concentrated crystal solution is transferred to the transfer tank, separated fro...
PUM
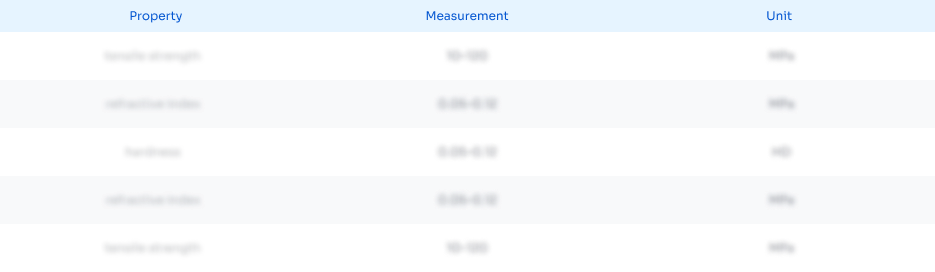
Abstract
Description
Claims
Application Information

- R&D Engineer
- R&D Manager
- IP Professional
- Industry Leading Data Capabilities
- Powerful AI technology
- Patent DNA Extraction
Browse by: Latest US Patents, China's latest patents, Technical Efficacy Thesaurus, Application Domain, Technology Topic, Popular Technical Reports.
© 2024 PatSnap. All rights reserved.Legal|Privacy policy|Modern Slavery Act Transparency Statement|Sitemap|About US| Contact US: help@patsnap.com