Near-zero stiffness vibration isolation system comprising combined magnetic negative stiffness mechanism
A vibration isolation system and negative stiffness technology, which is applied in the direction of shock absorbers, supporting machines, mechanical equipment, etc., can solve the problems of narrow stable area, deterioration of vibration isolation performance, and difficult installation and adjustment, so as to achieve small space cost and improve stability Effect
- Summary
- Abstract
- Description
- Claims
- Application Information
AI Technical Summary
Problems solved by technology
Method used
Image
Examples
Embodiment Construction
[0028] In order to make the object, technical solution and advantages of the present invention clearer, the present invention will be further described in detail below in conjunction with the accompanying drawings and embodiments. It should be understood that the specific embodiments described here are only used to explain the present invention, not to limit the present invention.
[0029] The present invention provides a near-zero-stiffness vibration isolation system including a combined magnetic negative stiffness mechanism. Its structural design is very reasonable and ingenious. The following describes its design principle in detail in conjunction with the drawings in the description:
[0030] figure 1 It is a schematic diagram of a near-zero stiffness vibration isolation system including a combined magnetic negative stiffness mechanism in an embodiment of the present invention, figure 2 It is the linear stiffness schematic diagram of the combined magnetic negative stiffn...
PUM
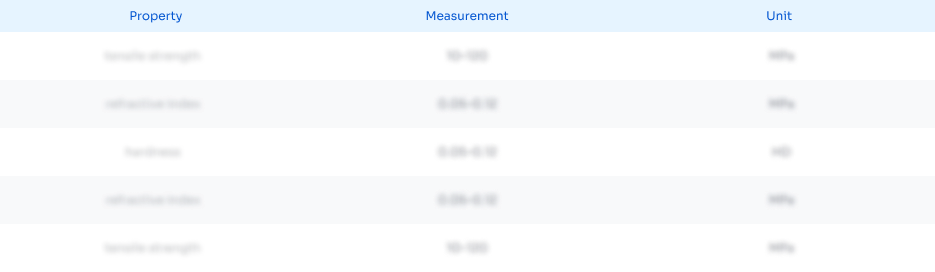
Abstract
Description
Claims
Application Information

- R&D
- Intellectual Property
- Life Sciences
- Materials
- Tech Scout
- Unparalleled Data Quality
- Higher Quality Content
- 60% Fewer Hallucinations
Browse by: Latest US Patents, China's latest patents, Technical Efficacy Thesaurus, Application Domain, Technology Topic, Popular Technical Reports.
© 2025 PatSnap. All rights reserved.Legal|Privacy policy|Modern Slavery Act Transparency Statement|Sitemap|About US| Contact US: help@patsnap.com