Method for circularly conditioning and dehydrating sludge
A sludge recycling and sludge technology, applied in sludge treatment, electrochemical sludge treatment, water/sludge/sewage treatment, etc., can solve the problems of unrealized dehydration and difficult treatment, and achieve good dehydration effect and equipment Ease of operation and improved dehydration performance
- Summary
- Abstract
- Description
- Claims
- Application Information
AI Technical Summary
Problems solved by technology
Method used
Image
Examples
Embodiment 1
[0020] The circulating sludge discharge pipe is located at 1 / 2 of the gravity concentration tank 3, and the mouth of the circulating sludge inlet pipe 1 is 30cm deeper than the nozzle of the fresh excess sludge inlet pipe 2.
[0021] Taking excess sludge with a water content of 98.2%-99.5% as the processing object, the excess sludge is injected into the gravity thickening tank 3 through the fresh excess sludge inlet pipe 2 . After the fresh excess sludge is concentrated in the gravity concentration tank 3 for 5 hours, the valve 10 on the circulating sludge discharge pipe is opened, so that the sludge in the layered sedimentation zone flows into the adjustment tank 5 under the action of gravity, and the sediment is passed through The mud discharge pipe 4 is discharged.
[0022] After the sludge in the stratified sedimentation zone flows into the regulating tank 5, sodium sulfate is added as an electrolyte, and the ratio of the added sodium sulfate to the sludge is 6 mg / L. Blas...
Embodiment 2
[0028] The circulating sludge discharge pipe is located at 1 / 2 of the gravity concentration tank 3, and the mouth of the circulating sludge inlet pipe 1 is 50 cm deeper than the nozzle of the fresh surplus sludge inlet pipe 2.
[0029] Taking excess sludge with a water content of 98.2%-99.5% as the processing object, the excess sludge is injected into the gravity thickening tank 3 through the fresh excess sludge inlet pipe 2 . After the fresh excess sludge is concentrated in the gravity concentration tank 3 for 5 hours, the valve 10 on the circulating sludge discharge pipe is opened, so that the sludge in the layered sedimentation zone flows into the adjustment tank 5 under the action of gravity, and the sediment is passed through The mud discharge pipe 4 is discharged.
[0030] After the sludge in the stratified sedimentation zone flows into the regulating tank 5, sodium sulfate is added as an electrolyte, and the ratio of the added sodium sulfate to the sludge is 6 mg / L. Bl...
Embodiment 3
[0036] The circulating sludge discharge pipe is located at 2 / 3 of the gravity thickening tank 3, and the mouth of the circulating sludge inlet pipe 1 is 80 cm deeper than the nozzle of the fresh surplus sludge inlet pipe 2.
[0037] Taking excess sludge with a water content of 98.2%-99.5% as the processing object, the excess sludge is injected into the gravity thickening tank 3 through the fresh excess sludge inlet pipe 2 . After the fresh excess sludge is concentrated in the gravity concentration tank 3 for 5 hours, the valve 10 on the circulating sludge discharge pipe is opened, so that the sludge in the layered sedimentation zone flows into the adjustment tank 5 under the action of gravity, and the sediment is passed through The mud discharge pipe 4 is discharged.
[0038] After the sludge in the stratified sedimentation zone flows into the regulating tank 5, sodium sulfate is added as an electrolyte, and the ratio of the added sodium sulfate to the sludge is 6 mg / L. Blast...
PUM
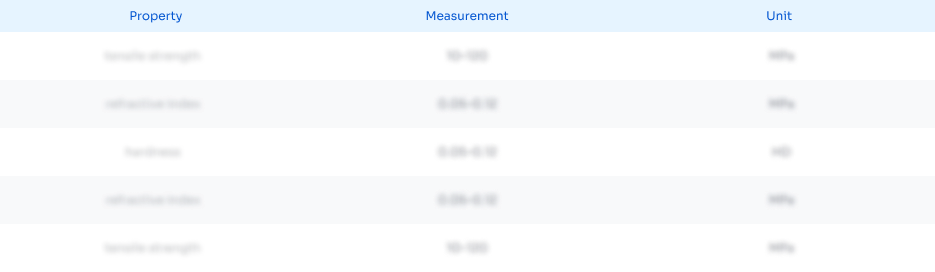
Abstract
Description
Claims
Application Information

- R&D Engineer
- R&D Manager
- IP Professional
- Industry Leading Data Capabilities
- Powerful AI technology
- Patent DNA Extraction
Browse by: Latest US Patents, China's latest patents, Technical Efficacy Thesaurus, Application Domain, Technology Topic, Popular Technical Reports.
© 2024 PatSnap. All rights reserved.Legal|Privacy policy|Modern Slavery Act Transparency Statement|Sitemap|About US| Contact US: help@patsnap.com