Method for preparing high-strength regenerated fiber paper through solution membrane casting method
A recycled fiber and high-strength technology, applied in the direction of textiles and papermaking, can solve the problems of insufficient use effect, insufficient tensile index, tear index and folding endurance of recycled fiber paper, and achieve novel design and application Good effect and reasonable process
- Summary
- Abstract
- Description
- Claims
- Application Information
AI Technical Summary
Problems solved by technology
Method used
Image
Examples
Embodiment 1
[0043] A method of preparing high-strength regenerated fiber paper by solution casting method of the present invention is as follows:
[0044] (1) commercially available unbleached eucalyptus pulp board fiber is broken into 1-3cm shredded paper;
[0045] (2) Add the shredded paper scraps described in the above step (1) to the 7% sodium hydroxide / 12% urea aqueous solution that has been pre-cooled to -13°C at a solid-to-liquid ratio of 1:25, and mechanically stir at 1500 rpm for 5 minutes;
[0046](3) Pour the heterogeneous mixed viscous solution obtained in the above step (2) into a polytetrafluoroethylene mold, spread it flat with a wire rod, defoam, put it in a blast drying oven at 60°C to remove the solvent, and solidify;
[0047] (4) Put the solid obtained in the above step (3) into a 20°C, 5% sulfuric acid / 5% sodium sulfate aqueous solution at 20°C with a solid-to-liquid ratio (g:ml) of 1:20, and let it stand for 5 minutes to reconstruct the hydrogen bond network , demoul...
Embodiment 2
[0050] A method of preparing high-strength regenerated fiber paper by solution casting method of the present invention is as follows:
[0051] (1) commercially available unbleached eucalyptus pulp board fiber is broken into 1-3cm shredded paper;
[0052] (2) Add the shredded paper scraps described in the above step (1) to the 7% sodium hydroxide / 12% urea aqueous solution that has been pre-cooled to -13°C at a solid-to-liquid ratio of 1:25, and mechanically stir at 20,000 rpm for 10 minutes;
[0053] (3) Pour the heterogeneous mixed viscous solution obtained in the above step (2) into a polytetrafluoroethylene mould, pave it with a wire rod, defoam, leave it at room temperature for 24 hours to remove the solvent, and solidify;
[0054] (4) Put the solid matter obtained in the above step (3) into room temperature and 5% sulfuric acid / 5% sodium sulfate aqueous solution with a solid-to-liquid ratio (g:ml) of 1:15 to 1:50 and let it stand for 5 minutes to carry out hydrogen bond ne...
Embodiment 3
[0057] A method of preparing high-strength regenerated fiber paper by solution casting method of the present invention is as follows:
[0058] (1) Commercially available unbleached eucalyptus pulp board fibers and commercially available unbleached Simao pine pulp board fibers are broken into 1-3cm shredded paper, and mixed uniformly with a mass ratio of 88:12;
[0059] (2) Add the mixed shredded paper scraps described in the above step (1) to the 7% sodium hydroxide / 12% urea aqueous solution that has been pre-cooled to -13°C at a solid-to-liquid ratio of 1:25, and mechanically stir at 2500rpm for 5min;
[0060] (3) Pour the heterogeneous mixed viscous solution obtained in the above step (2) into a polytetrafluoroethylene mold, spread it flat with a wire rod, defoam, and place it in a blast drying oven at 60°C for 4 hours to remove the solvent and solidify;
[0061] (4) Put the solid matter obtained in the above step (3) into room temperature and 7% ammonium sulfate aqueous sol...
PUM
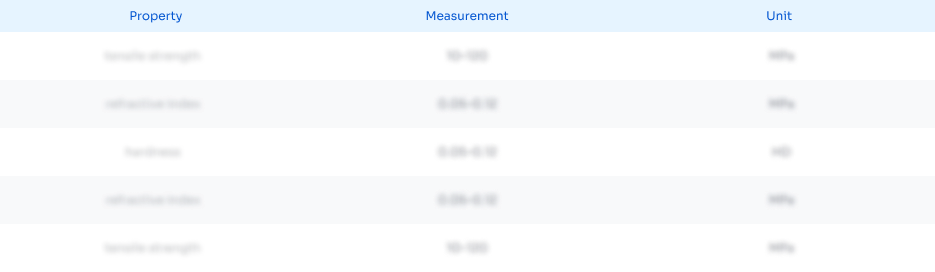
Abstract
Description
Claims
Application Information

- R&D Engineer
- R&D Manager
- IP Professional
- Industry Leading Data Capabilities
- Powerful AI technology
- Patent DNA Extraction
Browse by: Latest US Patents, China's latest patents, Technical Efficacy Thesaurus, Application Domain, Technology Topic, Popular Technical Reports.
© 2024 PatSnap. All rights reserved.Legal|Privacy policy|Modern Slavery Act Transparency Statement|Sitemap|About US| Contact US: help@patsnap.com