Mixing equipment for flame-retardant thermoplastic polyurethane elastomer
A thermoplastic polyurethane and mixing equipment technology, which is applied in the field of flame retardant material processing, can solve the problems of insufficient material mixing effect and too simple mixing and stirring structure, and achieve the effects of easy processing, stable structure, and guaranteed stability
- Summary
- Abstract
- Description
- Claims
- Application Information
AI Technical Summary
Problems solved by technology
Method used
Image
Examples
Embodiment 1
[0038] Example 1: See Figure 1-7 , a mixing device for flame-retardant thermoplastic polyurethane elastomers, comprising a device main body 4, the bottom end of the device main body 4 is fixedly connected with a top plate 3, the two sides of the bottom end of the top plate 3 are fixedly connected with support rods 16, and the bottom ends of the support rods 16 A bottom plate 1 is fixedly connected, a uniform discharge mechanism 2 is arranged between the top plate 3 and the bottom plate 1, a placement seat 8 is fixedly connected to the top of the equipment main body 4, and a feeding mechanism 9 is provided on the top side of the placement seat 8, and the inside of the placement seat 8 A crushing mechanism 7 is provided on one side of the device body 4, a heating mechanism 5 is provided on one side of the device body 4, a water inlet 6 is fixedly connected to the top of one side of the device body 4, and a mixing and stirring mechanism is provided inside the device body 4;
[0...
Embodiment 2
[0042] Embodiment 2: The uniform discharge mechanism 2 is composed of a first drive motor 201, a material guide pipe 202, a fixed seat 203, a screw conveying rod 204, and a discharge port 205. The fixed seat 203 is fixedly connected to the top of the bottom plate 1, and the fixed seat 203 The inner top runs through a feed pipe 202, and the top of the feed pipe 202 runs through the bottom end of the equipment main body 4, and the inside of the fixed seat 203 is connected with a screw conveying rod 204 horizontally, and one side of the screw conveying rod 204 passes through the shaft. The connector is fixedly connected to the output end of the first drive motor 201, the model of the first drive motor 201 can be Y90S-2, and the other side of the fixed seat 203 is fixedly connected with a discharge port 205;
[0043] Specifically, as figure 1 As shown, after the material processing is completed, the valve at the material guide pipe 202 is opened, and the first driving motor 201 is...
Embodiment 3
[0044] Embodiment 3: The heating mechanism 5 is composed of a connecting seat 501, an air intake fan 502, a ventilation pipe 503, a heating pipe 504, a duct 505, an air guide pipe 506, an isolation cover 507 and a distribution pipe 508, and the connecting seat 501 is fixedly connected to the bottom plate 1 One side of the connection seat 501 is fixedly connected with a heating pipe 504, the model of the heating pipe 504 can be HVL031-300W, the other side of the connection seat 501 is fixedly connected with a ventilation pipe 503, and one side of the ventilation pipe 503 is fixedly connected to There is an inlet fan 502, the type of the inlet fan 502 can be SF, one side of the connection seat 501 runs through a through pipe 505, two sets of through pipes 505 are provided, and the through pipes 505 are symmetrically distributed about the horizontal center line of the connection seat 501, The other side of the through pipe 505 runs through the interior of the device main body 4 an...
PUM
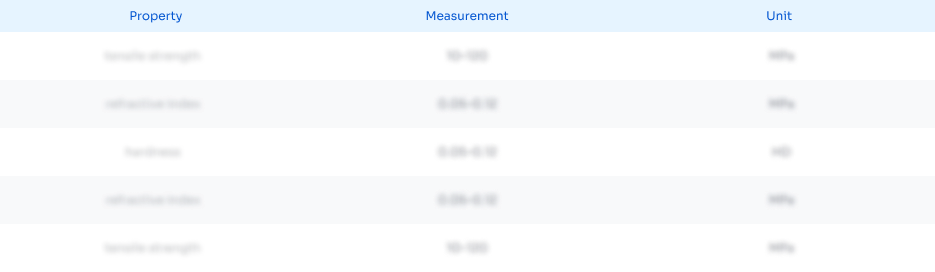
Abstract
Description
Claims
Application Information

- R&D
- Intellectual Property
- Life Sciences
- Materials
- Tech Scout
- Unparalleled Data Quality
- Higher Quality Content
- 60% Fewer Hallucinations
Browse by: Latest US Patents, China's latest patents, Technical Efficacy Thesaurus, Application Domain, Technology Topic, Popular Technical Reports.
© 2025 PatSnap. All rights reserved.Legal|Privacy policy|Modern Slavery Act Transparency Statement|Sitemap|About US| Contact US: help@patsnap.com