Flexible control method and system for multi-degree-of-freedom mechanical arm
A control method and technology for a control system, which are applied in the field of flexible control methods and systems for multi-degree-of-freedom robotic arms, can solve unsolved problems, and achieve the effects of improving work efficiency and ensuring safety.
- Summary
- Abstract
- Description
- Claims
- Application Information
AI Technical Summary
Problems solved by technology
Method used
Image
Examples
Embodiment 1
[0064] Such as figure 1 As shown, a multi-degree-of-freedom manipulator flexible control system includes: manipulator kinematics module, motion instruction module, trajectory planning module, load parameter identification module, force signal acquisition and compensation module, flexible control strategy module; the flexible control system It is suitable for multi-degree-of-freedom robotic arms. The multi-degree-of-freedom robotic arm contains several joints, and each joint is equipped with a motor; the robotic arm adopts one of the 6-axis industrial robotic arms or cooperative arms.
[0065] The kinematics module of the manipulator is used to model the kinematics of the manipulator, including a modeling unit and a forward and reverse kinematics unit; the modeling unit: according to the parameters of the connecting rod of the manipulator, the coordinate system of each joint is established by MDH , to obtain the homogeneous transformation matrix of two adjacent joint coordinate...
Embodiment 2
[0087] A method for flexible control of a multi-degree-of-freedom manipulator, comprising the steps of:
[0088](1) According to the connecting rod parameters of the manipulator, the joint coordinate system is established by MDH (ModifiedDenavitHartenberg) method, and the homogeneous transformation matrix of the two adjacent joint coordinate systems is obtained, and then the kinematic model of the manipulator is calculated; then according to the established manipulator The kinematics model realizes the mutual solution between the joint angle and the attitude value of the end position.
[0089] (2) Identify the load end parameters of the six-dimensional force sensor installed on the manipulator. By establishing the relationship equation between the load gravity component and the gravity moment component, read several groups of force sensor data under different postures at the end, and use the least square method to identify the load parameters. , the load parameters include the...
PUM
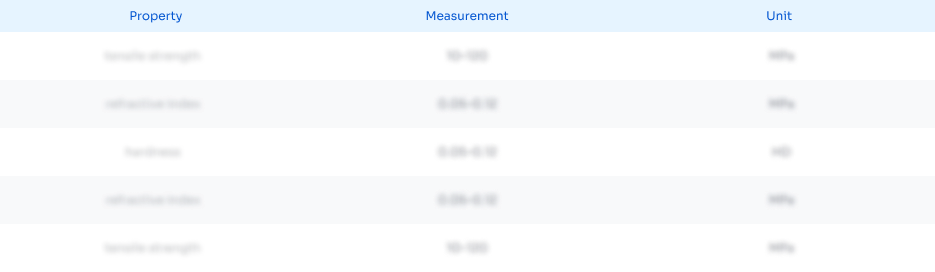
Abstract
Description
Claims
Application Information

- R&D
- Intellectual Property
- Life Sciences
- Materials
- Tech Scout
- Unparalleled Data Quality
- Higher Quality Content
- 60% Fewer Hallucinations
Browse by: Latest US Patents, China's latest patents, Technical Efficacy Thesaurus, Application Domain, Technology Topic, Popular Technical Reports.
© 2025 PatSnap. All rights reserved.Legal|Privacy policy|Modern Slavery Act Transparency Statement|Sitemap|About US| Contact US: help@patsnap.com