Vertical shaft cage guide flaw detection and deformation distributed optical fiber monitoring system and monitoring method
A technology of distributed optical fiber and monitoring system, which is applied to measurement devices, uses optical devices to transmit sensing components, and converts sensor outputs, etc. The effect of strong anti-interference ability and simple construction
- Summary
- Abstract
- Description
- Claims
- Application Information
AI Technical Summary
Problems solved by technology
Method used
Image
Examples
Embodiment
[0040] Embodiment: Using an integrated temperature and strain optical fiber as a sensor, and laying it in the small hole reserved inside the tank road 5, for monitoring the strain value and temperature value of the tank road 5, thereby measuring the temperature of the tank road 5 Flaw detection depth, deflection, strength, bending moment and torsion, etc., to know the condition of tank road 5 in time.
[0041] Such as Figure 1-2 As shown, the vertical shaft tank road 5 is a rectangular parallelepiped structure made by not less than one square steel pipe connected up and down, and its cross section is a square. One side of the tank road 5 is fixed by the tank road beam 7 and the mine wall 8, and the other three The wall is in frictional contact with the rubber wheel 6.
[0042] The installation of the flaw detection and deformation optical fiber distributed monitoring system of shaft tank 5, the specific steps are as follows:
[0043] (1) The tank road 5 is made of square ho...
PUM
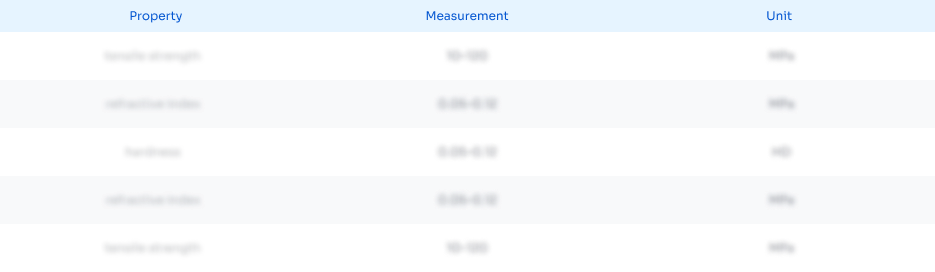
Abstract
Description
Claims
Application Information

- R&D Engineer
- R&D Manager
- IP Professional
- Industry Leading Data Capabilities
- Powerful AI technology
- Patent DNA Extraction
Browse by: Latest US Patents, China's latest patents, Technical Efficacy Thesaurus, Application Domain, Technology Topic, Popular Technical Reports.
© 2024 PatSnap. All rights reserved.Legal|Privacy policy|Modern Slavery Act Transparency Statement|Sitemap|About US| Contact US: help@patsnap.com