Asymmetric cutter module and plate bending device
An asymmetrical, cutting tool technology, applied in the direction of feeding device, positioning device, storage device, etc., to achieve the effect of increasing range, preventing mopping, and improving processing operability
- Summary
- Abstract
- Description
- Claims
- Application Information
AI Technical Summary
Problems solved by technology
Method used
Image
Examples
Embodiment 1
[0042] Such as Figure 5 and 6 As shown, a kind of asymmetric cutter module comprises: upper cutter 1 and lower molding die 2, and described upper cutter 1 comprises cutter body 11 and the cutter head 12 that is arranged on described cutter body 11 one end, and described cutter head 12 It includes two side walls arranged at an included angle, and the junction of the two side walls forms the tip of the cutter head 12, passing through the tip and parallel to the center line of the cutter body 11 in the height direction The included angles of the knife point vertical line 124 and the two side walls are different from each other; the lower forming die 2 comprises a forming die body and a forming groove 21 arranged at the upper end of the forming die body, and the forming groove 21 comprises two The forming side walls arranged at an included angle, the junction of the two forming side walls forms the bottom of the forming groove 21, the bottom of the groove passing through the bot...
Embodiment 2
[0049] This embodiment only describes the differences from the above embodiments, in this embodiment, such as Figure 9 As shown, the vertical line 124 of the knife tip does not coincide with the vertical line 213 at the bottom of the groove, and a distance ΔT is set between the vertical line 124 of the knife tip and the vertical line 213 at the bottom of the groove, so that the vertical line of the knife tip and the vertical line 213 of the groove bottom The groove bottom is arranged eccentrically.
[0050] The forming groove 21 includes a first forming side wall 211 and a second forming side wall 212, the intersection of the first forming side wall 211 and the lower end of the second forming side wall 212 forms the bottom of the groove, the first forming side wall 211 and the second forming side wall 212 form the groove bottom, The distance between the upper end of a forming side wall 211 and the vertical line 124 of the knife tip is VL, the distance between the upper end of...
Embodiment 3
[0052] This embodiment only describes the differences from the above embodiments. In this embodiment, an included angle is set between the cutter head 12 and the cutter body 11, and the cutter head 12 includes a first cutter head side wall 121, The second cutter head side wall 122, the first cutter head side wall 121 and the second cutter head side wall 122 are arranged at an angle, the lower end of the first cutter head side wall 121 is connected to the second cutter head The intersection of the lower ends of the side walls 122 forms the tip of the cutter head 12 , and the upper end of the first cutter head side wall 121 and the upper end of the second cutter head side wall 122 extend upward to form two opposite sets of the cutter body 11 . side wall. Such setting can make the molding process of the cutter head 12 simple and the manufacturing cost low.
PUM
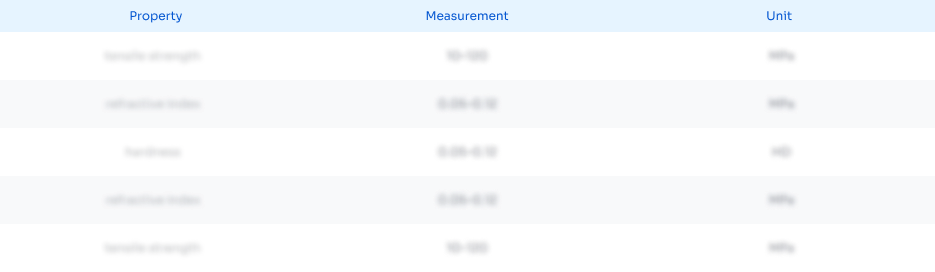
Abstract
Description
Claims
Application Information

- R&D
- Intellectual Property
- Life Sciences
- Materials
- Tech Scout
- Unparalleled Data Quality
- Higher Quality Content
- 60% Fewer Hallucinations
Browse by: Latest US Patents, China's latest patents, Technical Efficacy Thesaurus, Application Domain, Technology Topic, Popular Technical Reports.
© 2025 PatSnap. All rights reserved.Legal|Privacy policy|Modern Slavery Act Transparency Statement|Sitemap|About US| Contact US: help@patsnap.com