Novel environment-friendly functional polypropylene and preparation method thereof
A technology for polypropylene and functionalization, which is applied in the field of new environmentally friendly functionalized polypropylene and its preparation, and can solve the problems of increased content of irritating volatiles in modified polypropylene, restrictions on the application of polypropylene materials, strong irritation and volatility, etc. , to achieve the effects of ensuring safety and health, reducing total migration and pungent odor, low volatility and irritation
- Summary
- Abstract
- Description
- Claims
- Application Information
AI Technical Summary
Problems solved by technology
Method used
Examples
Embodiment 1
[0022] In this embodiment, the preparation method of the novel environmentally friendly functionalized polypropylene comprises the following steps in sequence:
[0023] (1) By weight, the following raw materials are equipped: 99.42% polypropylene (both homopolypropylene), 0.08% organic peroxide (both 2,5-dimethyl-2,5-di(t-butyl peroxy) hexane), o-diallyl bisphenol A diglycidyl ether 0.50%;
[0024] (2) First mix the organic peroxy compound and o-diallyl bisphenol A diglycidyl ether to obtain a mixture A; then mix the mixture A with polypropylene to obtain a mixed material;
[0025] (3) Melt and extrude the mixed material through a twin-screw extruder, and the extruded material strands are cooled and then pelletized to obtain granular new environmentally friendly functional polypropylene.
[0026] The screw aspect ratio of the twin-screw extruder in the above step (3) is 48:1.
[0027] The temperature in the barrel of the twin-screw extruder in the above step (3) is 170-200°C...
Embodiment 2
[0029] In this embodiment, the preparation method of the novel environmentally friendly functionalized polypropylene comprises the following steps in sequence:
[0030] (1) By weight, equipped with the following raw materials: 98.38% polypropylene (both block copolymerized polypropylene), 0.12% organic peroxide (both tert-butyl peroxy-2-ethylhexanoate), o-diallyl bisphenol A diglycidyl ether 1.50%;
[0031] (2) First mix the organic peroxy compound and o-diallyl bisphenol A diglycidyl ether to obtain a mixture A; then mix the mixture A with polypropylene to obtain a mixed material;
[0032] (3) Melt and extrude the mixed material through a twin-screw extruder, and the extruded material strands are cooled and then pelletized to obtain granular new environmentally friendly functional polypropylene.
[0033] The screw aspect ratio of the twin-screw extruder in the above step (3) is 44:1.
[0034] The temperature in the barrel of the twin-screw extruder in the above step (3) is ...
Embodiment 3
[0036] In this embodiment, the preparation method of the novel environmentally friendly functionalized polypropylene comprises the following steps in sequence:
[0037] (1) By weight, the following raw materials are equipped: 97.30% polypropylene (both homopolypropylene), 0.20% organic peroxide (both 2,5-dimethyl-2,5-di(t-butyl peroxy) hexane), o-diallyl bisphenol A diglycidyl ether 2.50%;
[0038] (2) First mix the organic peroxy compound and o-diallyl bisphenol A diglycidyl ether to obtain a mixture A; then mix the mixture A with polypropylene to obtain a mixed material;
[0039] (3) Melting and extruding the mixed material through a twin-screw extruder, and cutting the extruded material into pellets after cooling to obtain a new type of environmentally friendly functional polypropylene in granular form.
[0040] The screw aspect ratio of the twin-screw extruder in the above step (3) is 52:1.
[0041] The temperature in the barrel of the twin-screw extruder in the above st...
PUM
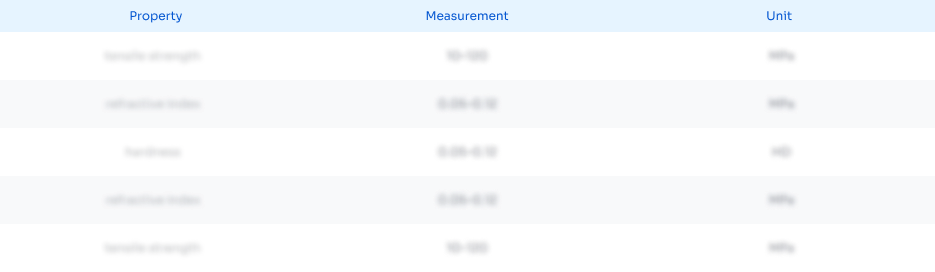
Abstract
Description
Claims
Application Information

- Generate Ideas
- Intellectual Property
- Life Sciences
- Materials
- Tech Scout
- Unparalleled Data Quality
- Higher Quality Content
- 60% Fewer Hallucinations
Browse by: Latest US Patents, China's latest patents, Technical Efficacy Thesaurus, Application Domain, Technology Topic, Popular Technical Reports.
© 2025 PatSnap. All rights reserved.Legal|Privacy policy|Modern Slavery Act Transparency Statement|Sitemap|About US| Contact US: help@patsnap.com