Necking and flaring mixed forming method for conical barrel part with straight barrel
A technology of conical cylinder and straight cylinder is applied in the field of flaring mixed forming, conical cylinder with straight cylinder and conical cylinder extrusion manufacturing, which can solve the problem of poor forging stability, large finished product allowance and material utilization rate. low problems, to achieve good dimensional accuracy, reduce metal grain growth, and simple methods
- Summary
- Abstract
- Description
- Claims
- Application Information
AI Technical Summary
Problems solved by technology
Method used
Image
Examples
Embodiment
[0036] Such as Figure 1-Figure 6 As shown, the shrinking and flaring hybrid forming method of the tapered cylindrical part in this embodiment is as follows:
[0037] Step 1: If figure 1 As shown, a steel pipe with a wall thickness of 180mm and an inner diameter of 730mm is machined and cut into a frustum-shaped and cylindrical integrated tube blank 6 of the required shape.
[0038] Among them, the truncated conical and cylindrical integrated tube blank 6 is a first truncated conical tube blank 61, cylindrical tube blank 62, and second conical truncated tube blank 65. Both are equal to 730mm. The outer diameter of the first frustum-shaped tube blank 61 is larger at the top and smaller at the bottom. The outer diameter of the upper end of the first frustum-shaped tube blank 61 is 1090mm, and the outer diameter of the lower end of the cylindrical tube blank 62 is 940mm. The height of the tube blank 61 is 850 mm; the outer diameter of the cylindrical tube blank 62 is the same a...
PUM
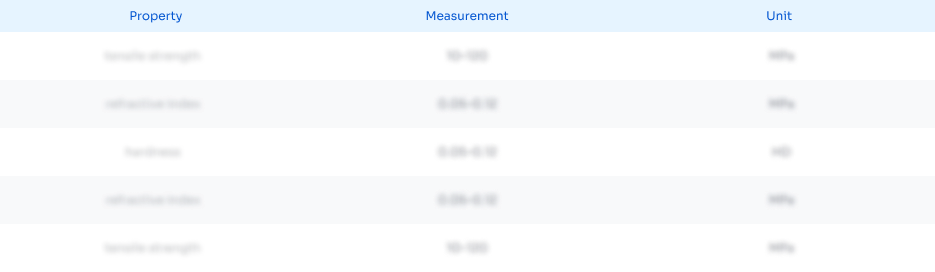
Abstract
Description
Claims
Application Information

- R&D
- Intellectual Property
- Life Sciences
- Materials
- Tech Scout
- Unparalleled Data Quality
- Higher Quality Content
- 60% Fewer Hallucinations
Browse by: Latest US Patents, China's latest patents, Technical Efficacy Thesaurus, Application Domain, Technology Topic, Popular Technical Reports.
© 2025 PatSnap. All rights reserved.Legal|Privacy policy|Modern Slavery Act Transparency Statement|Sitemap|About US| Contact US: help@patsnap.com