A Production Process for Increasing the Number of Continuous Casting Furnaces of Aluminum Deoxidized High Carbon Chromium Bearing Steel
An aluminum deoxidation high-carbon chromium bearing and production process technology, applied in the field of iron and steel metallurgy, can solve the problems of unqualified water immersion flaw detection and poor castability of bearing steel, so as to solve the problem of unqualified water immersion flaw detection and increase the number of continuous casting furnaces , Improve the effect of purity
- Summary
- Abstract
- Description
- Claims
- Application Information
AI Technical Summary
Problems solved by technology
Method used
Image
Examples
Embodiment
[0021] The test steel is high-carbon chromium bearing steel, the grade is GCr15, and the production process is "converter / electric furnace—LF refining—RH vacuum treatment—billet continuous casting":
[0022] (1) During the tapping process, aluminum grains are added for deoxidation at one time. It is required that the aluminum content in the steel be added to 0.03-0.06%. slag or slag removal;
[0023] (2) Add lime, quartz sand or CaO-Al to LF refining slag 2 o 3 It is one or several kinds of pre-melted slag, and it is required to ensure the final slag basicity of LF refining slag CaO / SiO 2 Control range 3.0~4.5, final slag CaO / Al 2 o 3 The control range is 1.3~2.5, the amount of refining slag added is 8~10kg / t, and the final slag is required to be 0.3%
[0024] (3) After the LF refining is completed, the molten steel is subjected to RH vacuum treatment according to the co...
PUM
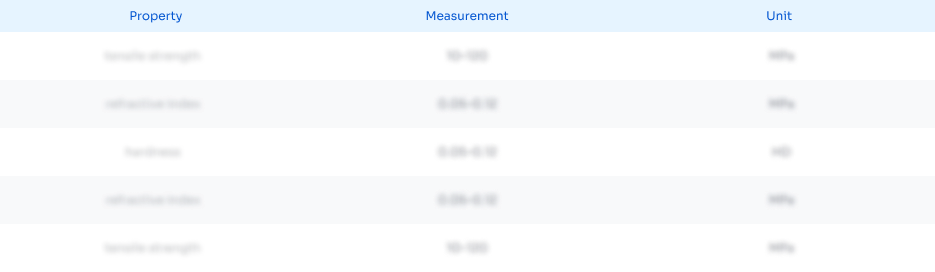
Abstract
Description
Claims
Application Information

- R&D
- Intellectual Property
- Life Sciences
- Materials
- Tech Scout
- Unparalleled Data Quality
- Higher Quality Content
- 60% Fewer Hallucinations
Browse by: Latest US Patents, China's latest patents, Technical Efficacy Thesaurus, Application Domain, Technology Topic, Popular Technical Reports.
© 2025 PatSnap. All rights reserved.Legal|Privacy policy|Modern Slavery Act Transparency Statement|Sitemap|About US| Contact US: help@patsnap.com