Method for controlling zinc load of blast furnace
A load and blast furnace technology, applied in the field of smelting, can solve problems such as furnace wall bonding, damage to blast furnace lining, and reduce thermal strength of coke, so as to achieve the effects of ensuring stable production, ensuring effective utilization, and reducing production costs
- Summary
- Abstract
- Description
- Claims
- Application Information
AI Technical Summary
Problems solved by technology
Method used
Image
Examples
Embodiment
[0069] Embodiment: A steel mill adopts this method to control the zinc load of blast furnace fuel, specifically as follows.
[0070] (1) Determine the zinc load index of the furnace to be controlled at Zn (∝) = 300 g / t.
[0071] (2) The furnace charge structure is 10wt% of South African ore, 65wt%≤A≤68wt% of sintered ore, and 25wt%≥B≥22wt% of pellet ore.
[0072] The furnace zinc load in South African mines is calculated by the formula (I): Zn (w) =ω1 (Zn) *106 / (ω1 (Fe) *0.99 / 0.945), where ω1 (Zn) =0.002%, ω1 (Fe) =64.1%, into the above formula to get Zn (w) = 29.78 g / t.
[0073] (3) The comprehensive fuel ratio of the steel plant k=500kg / t, calculated by the formula (II): Zn (R) =k*1000*A*ω2 (Zn) , where A=12.5%, ω2 (Zn) =0.071%, brought into the above formula to get Zn (R) = 39.94 g / t.
[0074] (4) The total amount of zinc load Zn allowed to be brought into the blast furnace by sinter and pellets (Z) Calculated by formula (Ⅲ): Zn (Z) =300-Zn (w) *10%-Zn (R) ,...
PUM
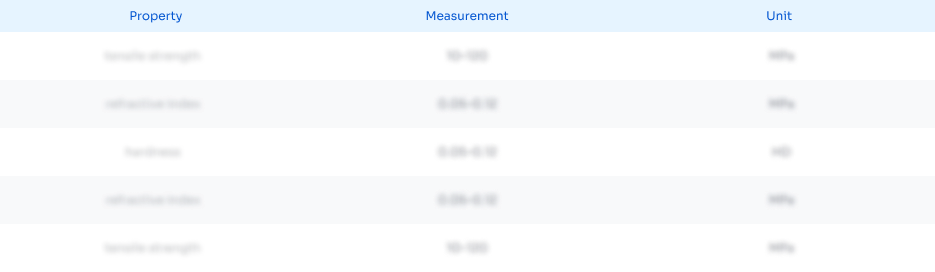
Abstract
Description
Claims
Application Information

- R&D Engineer
- R&D Manager
- IP Professional
- Industry Leading Data Capabilities
- Powerful AI technology
- Patent DNA Extraction
Browse by: Latest US Patents, China's latest patents, Technical Efficacy Thesaurus, Application Domain, Technology Topic, Popular Technical Reports.
© 2024 PatSnap. All rights reserved.Legal|Privacy policy|Modern Slavery Act Transparency Statement|Sitemap|About US| Contact US: help@patsnap.com