Decoupling variable-rigidity joint suitable for super-redundant mechanical arm
A technology of robotic arms and joints, applied in the field of robotics, can solve problems such as difficult decoupling and insufficient rigidity
- Summary
- Abstract
- Description
- Claims
- Application Information
AI Technical Summary
Problems solved by technology
Method used
Image
Examples
Embodiment Construction
[0018] Embodiments of the present invention will be described in detail below in conjunction with the accompanying drawings.
[0019] attached figure 1 It is a schematic diagram of the structure of a decoupled variable stiffness joint suitable for super-redundant manipulators in the present invention. The joint is composed of a hollow connecting rod 1, upper and lower fixed plates 2, 2 , , three hollow organ type variable stiffness drivers 3, a sleeve 4, and a universal joint mechanism 5. Lower fixed plate 2 , Installed to the lower end of the hollow connecting rod 1 through screws, the lower end of the upper fixed plate 2 is installed on the upper end of the hollow connecting rod 1 through screws; the lower end of the sleeve 4 is installed outside the central control connecting rod 1 and stuck on the lower fixed plate 2 , On the boss, the upper end of the sleeve 4 is installed and stuck on the lower boss of the upper fixed disk 2; the upper and lower fixed disks 2 and 2 , ...
PUM
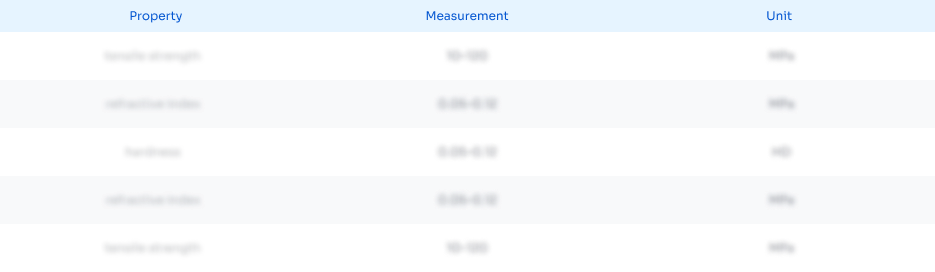
Abstract
Description
Claims
Application Information

- R&D
- Intellectual Property
- Life Sciences
- Materials
- Tech Scout
- Unparalleled Data Quality
- Higher Quality Content
- 60% Fewer Hallucinations
Browse by: Latest US Patents, China's latest patents, Technical Efficacy Thesaurus, Application Domain, Technology Topic, Popular Technical Reports.
© 2025 PatSnap. All rights reserved.Legal|Privacy policy|Modern Slavery Act Transparency Statement|Sitemap|About US| Contact US: help@patsnap.com