Centralized 3D printing control system and control method
A 3D printing and control system technology, applied in the direction of digital output to printing units, instruments, calculations, etc., can solve problems such as poor real-time performance and cumbersome process
- Summary
- Abstract
- Description
- Claims
- Application Information
AI Technical Summary
Problems solved by technology
Method used
Image
Examples
Embodiment 1
[0021] The central server control terminal is controlled by the queue dispatcher, and the upper computer control terminal accepts the commands sent by the central server control terminal through wired or wireless means, and transmits its own status back to the queue dispatcher in real time.
[0022] The queue dispatcher is used to control the production sequence and production flow.
[0023] The data collection server is used to collect and analyze all data generated in the system.
[0024] The state monitoring workstation is used for displaying production arrangement and operation state information of 3D printing equipment.
[0025] The order management workstation is used as a transaction system connecting users and merchants, accepting customer order information and displaying processing status information.
[0026] The node printing controller is used to prefetch and check the stored pre-execution tasks according to preset verification standards, and when the instruction ...
Embodiment 2
[0034] The difference between this embodiment and Embodiment 1 is: the 3D printing control system also includes an image acquisition device, an ultrasonic flaw detection device, and a photoelectric feedback device; the feedback device is connected to the node printing control machine for monitoring the working status of the 3D printing device, and sending the working status to the node printing control machine; the queue scheduler is used to receive the working status of the node printing control machine, and broadcast the working status To each type for users to view.
PUM
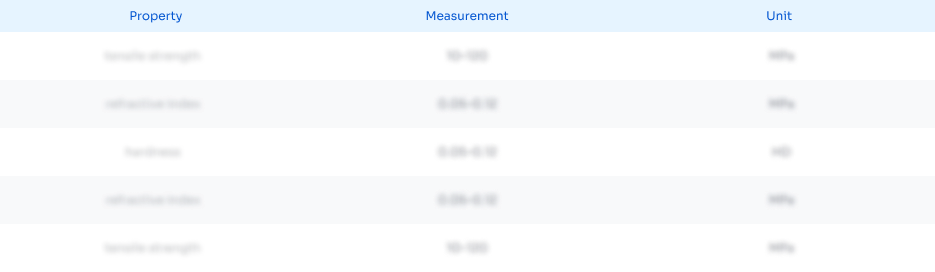
Abstract
Description
Claims
Application Information

- R&D Engineer
- R&D Manager
- IP Professional
- Industry Leading Data Capabilities
- Powerful AI technology
- Patent DNA Extraction
Browse by: Latest US Patents, China's latest patents, Technical Efficacy Thesaurus, Application Domain, Technology Topic, Popular Technical Reports.
© 2024 PatSnap. All rights reserved.Legal|Privacy policy|Modern Slavery Act Transparency Statement|Sitemap|About US| Contact US: help@patsnap.com