Weld joint reinforcement automatic milling device and path generation method and using method
A technology of automatic milling and weld reinforcement, applied in the direction of manipulators, program-controlled manipulators, manufacturing tools, etc., can solve problems such as difficulties
- Summary
- Abstract
- Description
- Claims
- Application Information
AI Technical Summary
Problems solved by technology
Method used
Image
Examples
specific example 1
[0043] The material is 16Mn, the shape is plate-like, and the workpiece 21 to be processed is 1m long, 0.5m wide, and 10mm thick. , the to-be-milled weld 23 is a linear weld with a length of 1 m. Such as Image 6 As shown, the surface of the workpiece 21 to be processed that needs to have weld reinforcement removed is the pseudo-milling surface 24 . The width of the fusion width 25 of the to-be-milled weld on the to-be-milled surface is 13-15mm, and the height of the to-be-milled weld's reinforcement 26 on the to-be-milled surface is 4-6mm, which needs to be removed after welding.
[0044] First teach robot 1, such as image 3 As shown, before teaching, it is necessary to install the teaching thimble 9 on the milling path pick-up module 3, and prepare a standard workpiece 27. The standard workpiece 27 adopts a base material 22 of the same specification, that is, a 1m long, 0.25m wide, and 10mm thick steel plate. Place the standard workpiece 27 on the console 28, install an...
specific example 2
[0051] The material is Q235, the shape is semi-tubular, and the size specification is 10m in length, 0.25m in radius, and 12mm in thickness. The proposed milling weld is a semi-circular weld with a length of 0.785m. The concave surface of the processed workpiece is the pseudo-milling surface. The width of the fusion width of the to-be-milled weld on the to-be-milled surface is 15-17mm, and the height of the reinforcement of the to-be-milled weld to be located on the to-be-milled surface is 5-7mm, which needs to be removed after welding.
[0052] In this example: (1) The standard workpiece adopts a base material of the same specification, that is, a semi-tubular base material with a length of 5m, a radius of 0.25m, and a thickness of 12mm. (2) Special fixtures are required for positioning and clamping Standard workpieces and processed workpieces. Except that the above two places are different, other places are all the same as the method adopted in concrete example 1.
specific example 3
[0054] The material is 6061 aluminum alloy, the shape is wavy, and the size specification is 1m in length, 0.8m in width, and 6mm in thickness. It is tailor-welded along the length direction, and the to-be-milled weld is a wavy weld, which is 1.5m long after straightening. The surface on which the weld reinforcement needs to be removed on the processed workpiece is the pseudo-milling surface. The width of the fusion width of the to-be-milled weld on the to-be-milled surface is 10-13mm, and the height of the reinforcement of the to-be-milled weld to be located on the to-be-milled surface is 3-4mm, which needs to be removed after welding.
[0055] In this example: (1) The standard workpiece adopts a base material of the same specification, that is, a wavy base material with a length of 1m, a width of 0.4m, and a thickness of 6mm. (2) Special fixtures are required to position and clamp the standard workpiece and Workpiece to be processed. Except that the above two places are di...
PUM
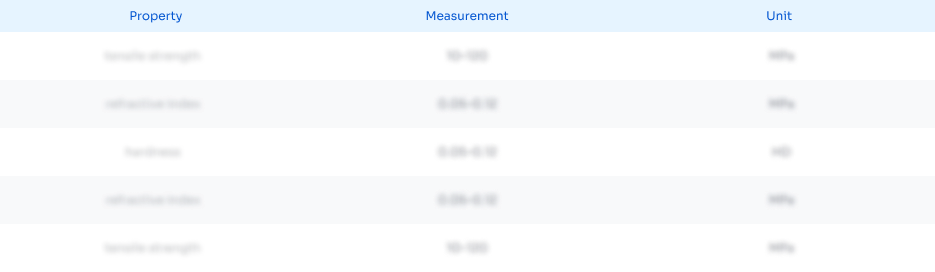
Abstract
Description
Claims
Application Information

- Generate Ideas
- Intellectual Property
- Life Sciences
- Materials
- Tech Scout
- Unparalleled Data Quality
- Higher Quality Content
- 60% Fewer Hallucinations
Browse by: Latest US Patents, China's latest patents, Technical Efficacy Thesaurus, Application Domain, Technology Topic, Popular Technical Reports.
© 2025 PatSnap. All rights reserved.Legal|Privacy policy|Modern Slavery Act Transparency Statement|Sitemap|About US| Contact US: help@patsnap.com