A method for controlling inclusions in a bearing steel refining furnace process
A refining furnace and bearing steel technology, applied in the field of steelmaking, can solve the problems of insufficient performance and service life of bearing steel, and achieve the effects of reducing the smelting cycle and ladle erosion time, controlling inclusions, and reducing noise.
- Summary
- Abstract
- Description
- Claims
- Application Information
AI Technical Summary
Problems solved by technology
Method used
Examples
Embodiment 1
[0053] This embodiment provides a method for controlling inclusions in a bearing steel refining furnace process, the method comprising:
[0054] The blast furnace molten iron is successively subjected to converter smelting, deoxidation alloying, LF refining and VD vacuum refining;
[0055] Wherein, the control slag system in the deoxidation alloying includes, in terms of mass percentage: CaO 50%, Al 2 O 3 27%, SiO 2 5%, MgO 6%; slag washing material is added in the deoxidation alloying; the slag washing material includes high-activity lime, high-aluminum refining slag and aluminum material; the content of effective calcium oxide in the high-activity lime is 98% The addition of high-activity lime in the slag washing material is 3.5kg / ton of molten iron; the aluminum in the high-alumina refining slag is 40% by mass percentage; the addition of the high-alumina refining slag in the slag washing material is 12kg / ton of molten iron; the addition of aluminum material in the slag ...
Embodiment 2
[0060] This embodiment provides a method for controlling inclusions in a bearing steel refining furnace process, the method comprising:
[0061] The blast furnace molten iron is successively subjected to converter smelting, deoxidation alloying, LF refining and VD vacuum refining;
[0062] Wherein, the control slag system in the deoxidation alloying includes, in terms of mass percentage: CaO 55%, Al 2 O 3 30%, SiO 2 6%, MgO 7%; slag washing material is added in the deoxidation alloying; the slag washing material includes high-activity lime, high-aluminum refining slag and aluminum material; the content of effective calcium oxide in the high-activity lime is 92% The addition of high-activity lime in the slag washing material is 5kg / ton of molten iron; the aluminum in the high-alumina refining slag is 50% by mass percentage; the addition of the high-alumina refining slag in the slag washing material is 15kg / ton of molten iron; the addition of aluminum material in the slag ...
Embodiment 3
[0067] This embodiment provides a method for controlling inclusions in a bearing steel refining furnace process, the method comprising:
[0068] The blast furnace molten iron is successively subjected to converter smelting, deoxidation alloying, LF refining and VD vacuum refining;
[0069] Wherein, the control slag system in the deoxidation alloying includes, in terms of mass percentage: CaO 45%, Al 2 O 3 25%, SiO 24%, MgO 5%; slag washing material is added in the deoxidation alloying; the slag washing material includes high-activity lime, high-alumina refining slag and aluminum material; the content of effective calcium oxide in the high-activity lime is 94% The addition of high-activity lime in the slag washing material is 2.5kg / ton of molten iron; the aluminum in the high-alumina refining slag is 45% by mass; the addition of the high-alumina refining slag in the slag washing material is 10kg / ton of molten iron; the addition of aluminum material in the slag washing materi...
PUM
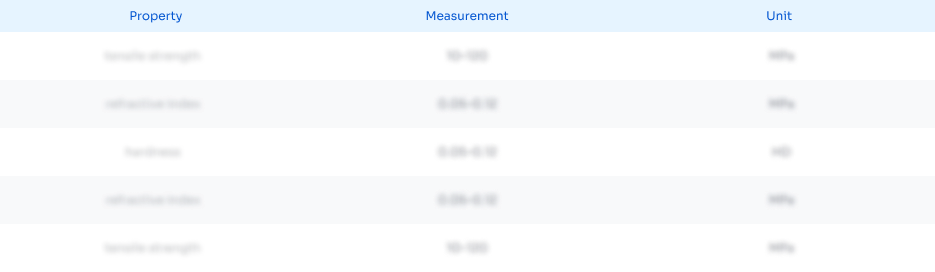
Abstract
Description
Claims
Application Information

- R&D Engineer
- R&D Manager
- IP Professional
- Industry Leading Data Capabilities
- Powerful AI technology
- Patent DNA Extraction
Browse by: Latest US Patents, China's latest patents, Technical Efficacy Thesaurus, Application Domain, Technology Topic, Popular Technical Reports.
© 2024 PatSnap. All rights reserved.Legal|Privacy policy|Modern Slavery Act Transparency Statement|Sitemap|About US| Contact US: help@patsnap.com