Casting method of high-speed high-power diesel engine cylinder cover
A high-power diesel engine and cylinder head technology, applied in the direction of casting molding equipment, casting molds, casting mold components, etc., can solve the problems of poor filter residue effect, poor sand mold compactness and rigidity, slow cooling speed, etc., to reduce porosity Defects, reduce porosity defects, avoid the effect of heat concentration
- Summary
- Abstract
- Description
- Claims
- Application Information
AI Technical Summary
Problems solved by technology
Method used
Image
Examples
Embodiment 1
[0045] A casting method for the cylinder head of a high-speed and high-power diesel engine, which can reduce inclusions, pores and loose defects of the cylinder head, improve the internal quality of the cylinder head, and reduce the leakage rate, such as figure 1 , figure 2 , image 3 As shown, specifically set to the following structure:
[0046] Basically, the casting method of this kind of high-speed and high-power diesel engine cylinder head adopts one mold and two pieces for production, so that the two pieces of cylinder head cavities in the sand mold are arranged side by side. The pouring system in the mold used by this method needs to use The molten metal flows downward from the sand mold located on the center line between the two cylinder heads, close to the side of the exhaust end face, and makes the metal liquid be located between the two cylinder head cavities at the exhaust end face The positions in between flow to the left and right respectively and enter the c...
Embodiment 2
[0060] This embodiment is further optimized on the basis of the foregoing embodiments, and particularly adopts the following configuration structure:
[0061] In step S3, determine the line connecting the centers of the two cylinder heads, that is, the center line 9 of the cylinder head is located on one side of the center line 8 in the length direction of the sand mold as a whole, and there are castings, runners and ingates in the width direction of the sand mold. The center line of the cover is offset to one side to reserve a place for the gating system design on the other side, avoiding one side being too close to the edge.
[0062] The centerline 9 of the two cylinder heads is on one side of the centerline 8 in the sand mold length direction, with an offset of 30mm. See figure 1 .
Embodiment 3
[0064] This embodiment is further optimized on the basis of the above-mentioned embodiment, and particularly adopts the following setting structure: In step S4, determine that the number of inrunners of a single cylinder head is set to two, so that the position of the inrunner of a single cylinder head Two locations in the lateral direction of the exhaust end face. A single cylinder head is equipped with two inrunners 6, so that less molten metal flows through a single inrunner 6, which can reduce the edge of the inrunner 6 from being scoured by the molten metal, and prevent the core near the inrunner 6 from being washed away. Sand inclusion defects or even leakage will occur in the cylinder head; in addition, when the two ingates are poured, the heat near the single ingate 6 is relatively small, so as to avoid local overheating and reduce the tendency of loose defects. In order to increase the cooling speed of the exhaust end face and ensure the overall uniform solidification...
PUM
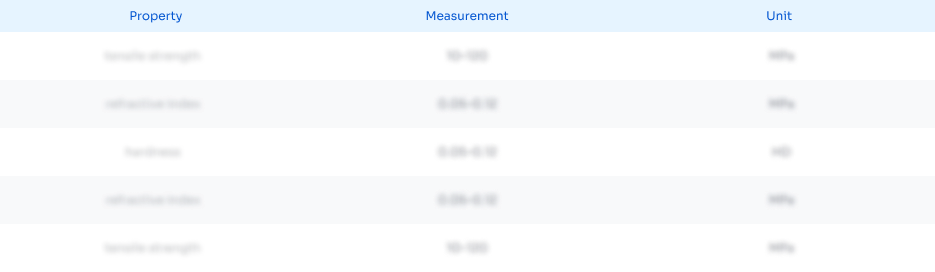
Abstract
Description
Claims
Application Information

- Generate Ideas
- Intellectual Property
- Life Sciences
- Materials
- Tech Scout
- Unparalleled Data Quality
- Higher Quality Content
- 60% Fewer Hallucinations
Browse by: Latest US Patents, China's latest patents, Technical Efficacy Thesaurus, Application Domain, Technology Topic, Popular Technical Reports.
© 2025 PatSnap. All rights reserved.Legal|Privacy policy|Modern Slavery Act Transparency Statement|Sitemap|About US| Contact US: help@patsnap.com