Device and method for granulating blast furnace slag and recycling waste heat
A waste heat recovery and blast furnace slag technology, which is applied in recycling technology, steam engine devices, lighting and heating equipment, etc., can solve problems such as high equipment cost and energy consumption, secondary pollution of air and water sources, and low treatment efficiency
- Summary
- Abstract
- Description
- Claims
- Application Information
AI Technical Summary
Problems solved by technology
Method used
Image
Examples
preparation example Construction
[0067] The preparation steps of described high temperature steam are:
[0068] Step 4.2.1: The cyclone separator 8 transports the high temperature granular slag 6 to the high temperature granular slag conveyor 21 . After being fed into the high temperature slag heat exchanger 22, the high temperature granulated slag 6 moves from top to bottom, and in the process of descending, it is in countercurrent contact with the cooling water in the coil and the air from bottom to top to exchange heat.
[0069] Step 4.2.2: The heated high temperature steam is discharged from the top of the high temperature granular slag heat exchanger 22 and sent to the boiler 23, and the cooled granular slag is discharged into the slag bin 11 from the lower part of the high temperature granular slag heat exchanger. The temperature of the slag after cooling is below 200°C.
[0070] Step 4.2.3: The external pipe network sends the pure water to the economizer 24, and is preheated to above 80°C by the mediu...
Embodiment 1
[0078] Please see attached figure 1 , When the blast furnace is tapping, the blast furnace slag enters the main ditch along with the molten iron from the tap hole, and is divided by the slag stopper. The molten slag at 1450-1550 ℃ is separated from the molten iron and enters the slag slag ditch, and then enters the aerosol granulation nozzle. The components are granulated: the slag flow 1 flows out after being controlled by the slag flow controller 2. After the slag flow 1 is separated from the slag flow controller 2, the high-pressure aerosol sprayed by the aerosol spray gun 5 is sprayed during the falling process. Blown, granulated and preliminarily cooled to form high temperature granular slag 6 at 1000-1200 °C and medium temperature gas at 200-400 °C. The flow rate of the high-pressure aerosol is determined by the compressed air flow control valve 3 and the water quantity control valve 4, and is automatically adjusted within a certain range with the size of the slag flow 1...
Embodiment 2
[0083] Please see attached figure 2 , When the blast furnace is tapping, the blast furnace slag enters the main ditch along with the molten iron from the tap hole, and is divided by the slag stopper. The molten slag at 1450-1550 ℃ is separated from the molten iron and enters the slag slag ditch, and then enters the aerosol granulation nozzle. The components are granulated: the slag flow 1 flows out after being controlled by the slag flow controller 2. After the slag flow 1 is separated from the slag flow controller 2, the high-pressure aerosol sprayed by the aerosol spray gun 5 is sprayed during the falling process. Blown, granulated and preliminarily cooled to form high temperature granular slag 6 at 1000-1200 °C and medium and high temperature gas at 200-400 °C. The flow rate of the high-pressure aerosol is determined by the compressed air flow control valve 3 and the water quantity control valve 4, and is automatically adjusted within a certain range with the size of the s...
PUM
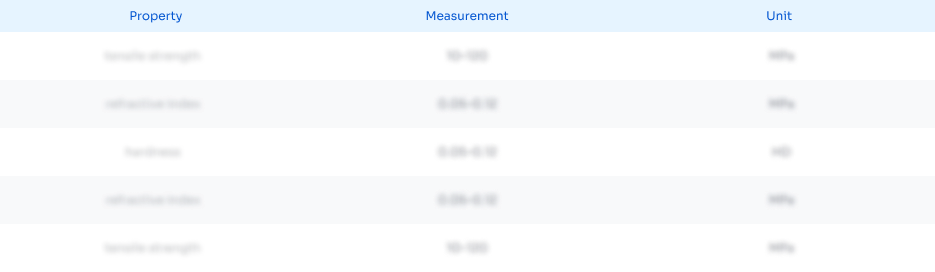
Abstract
Description
Claims
Application Information

- R&D
- Intellectual Property
- Life Sciences
- Materials
- Tech Scout
- Unparalleled Data Quality
- Higher Quality Content
- 60% Fewer Hallucinations
Browse by: Latest US Patents, China's latest patents, Technical Efficacy Thesaurus, Application Domain, Technology Topic, Popular Technical Reports.
© 2025 PatSnap. All rights reserved.Legal|Privacy policy|Modern Slavery Act Transparency Statement|Sitemap|About US| Contact US: help@patsnap.com