Thermally conductive composite filler, high thermally conductive composite material and preparation method thereof
A technology of composite materials and thermally conductive fillers, applied in the direction of heat exchange materials, chemical instruments and methods, etc., can solve the problems of high cost, low thermal conductivity, high density, etc.
- Summary
- Abstract
- Description
- Claims
- Application Information
AI Technical Summary
Problems solved by technology
Method used
Image
Examples
preparation example Construction
[0046] At present, the commonly used preparation methods of high thermal conductivity composite materials are to mix thermally conductive fillers with three-dimensional structures with polymers by direct mixing (melt kneading, direct mechanical mixing, etc.).
[0047] However, these direct mixing methods destroy the original three-dimensional structure of the thermally conductive fillers (due to the lack of support inside the three-dimensional fillers), such as compressing the three-dimensional structure into a two-dimensional structure, reducing the contact area between the thermally conductive fillers, and the interior of the three-dimensional structure of the thermally conductive fillers. The pores or gaps are very small, usually micron or even nanoscale. Direct mixing can easily cause the polymer to be insufficiently filled inside the thermally conductive filler and leave air, resulting in an unsatisfactory thermal conductivity improvement rate, which further leads to the th...
Embodiment 1
[0074] Step (1): 5.7g of expanded graphite, 0.1g of graphene, 1.7g of nano-alumina and 7.5g of polyphenylene sulfide are placed in dimethylformamide, stirred evenly, heated to 155°C to remove dimethylformamide, and obtained Thermally conductive composite filler.
[0075] Step (2): put the thermally conductive composite filler obtained in step (1) and 10g of polyphenylene sulfide in a material cup, and stir and strengthen the mixing by planetary stirring to obtain a mixture;
[0076] Step (3): The mixture is placed in different molds and hot-pressed. Hot pressing conditions: temperature 160℃~260℃, heat preservation for 35min; pressurization once, pressure 19MPa, pressure relief after 0.5min; secondary pressurization, pressure 19MPa, pressure relief after holding pressure for 3.5min; pressurization three times, pressure relief 19MPa, pressure relief after 11min holding pressure; four times of pressure, pressure 19MPa, pressure relief after holding pressure for 40min. Cooling t...
Embodiment 2
[0078] Step (1): 2.4g of expanded graphite, 0.1g of nano-silicon carbide and 12.5g of polyethersulfone are placed in dimethylformamide and stirred evenly, heated to 155° C. to remove dimethylformamide to obtain a thermally conductive composite filler.
[0079] Step (2): The thermally conductive composite filler obtained in step (1) and 10g of polyethersulfone are placed in a material cup, and planetary stirring is strengthened to mix to obtain a mixture;
[0080] Step (3): The mixture is placed in different molds and hot-pressed, and the hot-pressing conditions are the same as those of Comparative Example 1. Cooling to obtain a high thermal conductivity composite material.
PUM
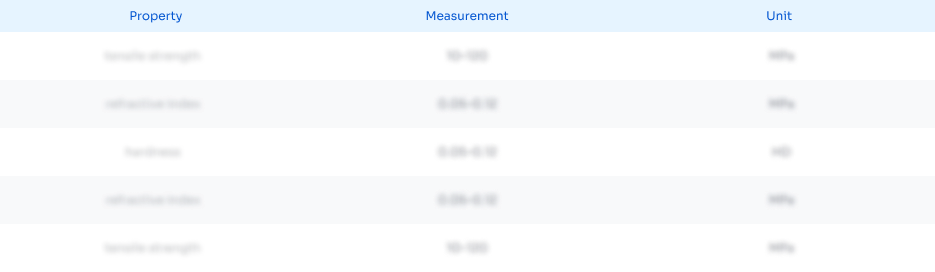
Abstract
Description
Claims
Application Information

- R&D Engineer
- R&D Manager
- IP Professional
- Industry Leading Data Capabilities
- Powerful AI technology
- Patent DNA Extraction
Browse by: Latest US Patents, China's latest patents, Technical Efficacy Thesaurus, Application Domain, Technology Topic.
© 2024 PatSnap. All rights reserved.Legal|Privacy policy|Modern Slavery Act Transparency Statement|Sitemap