Refining method of epoxy resin
A technology of epoxy resin and refining method, applied in the field of chemical refining, can solve the problems of increasing the production cost of epoxy resin, generating epoxy pressure, etc., to reduce production processing cost and raw material consumption, reduce organic content, and avoid excessive condensation. Effect
- Summary
- Abstract
- Description
- Claims
- Application Information
AI Technical Summary
Problems solved by technology
Method used
Image
Examples
Embodiment 1
[0061] Take 1000g of crude resin after removing epichlorohydrin, and measure its hydrolyzable chlorine content by GB / T4618.2-2008 saponifiable chlorine content detection method to be 16250ppm, wherein: the quality of the NaCl contained is 360g, the epoxy contained The quality of resin is 640g;
[0062] According to the ratio of the total amount of substance of sodium hydroxide and the amount of substance of the chloride ion in the hydrolyzable chlorine in the described thick epoxy resin, be 1.2:1, calculate the consumption 14.3g of required sodium hydroxide, therefore, get 14.3 g sodium hydroxide is made into mass concentration and is 28.6g of 50% sodium hydroxide solution;
[0063] (1) 1000g thick resin and 430g toluene are mixed and heated up to 90°C, then add 1.2g benzyltriethylammonium chloride (mass fraction 50%) to obtain a mixed solution; the mass of the thick resin in the mixed solution The content is 60%;
[0064] (2) Mix the mixed solution obtained in the step (1) ...
Embodiment 2
[0074] Take 1000g of the crude resin after removal of epichlorohydrin, and measure its hydrolyzable chlorine content by GB / T4618.2-2008 saponifiable chlorine content detection method to be 184670ppm, wherein: the quality of the NaCl contained is 360g, and the epoxy The mass of resin is 634g;
[0075] According to the ratio of the total substance amount of sodium hydroxide and the amount of substance of the chloride ion in the hydrolyzable chlorine in the described thick epoxy resin, be 1.15:1, calculate the consumption 15.6g of required sodium hydroxide, therefore, get 15.6 gNaOH is made into mass concentration and is 31.2g of 50% sodium hydroxide solution;
[0076] (1) After mixing 1000g of crude resin and 640g of toluene, heat up to 90°C, then add 10g of polyethylene glycol 200 (50% by mass fraction) to obtain a mixed solution; the mass content of the crude resin in the mixed solution is 60% ;
[0077] (2) Mix the mixed solution obtained in the step (1) with 12.4 g of 50% ...
PUM
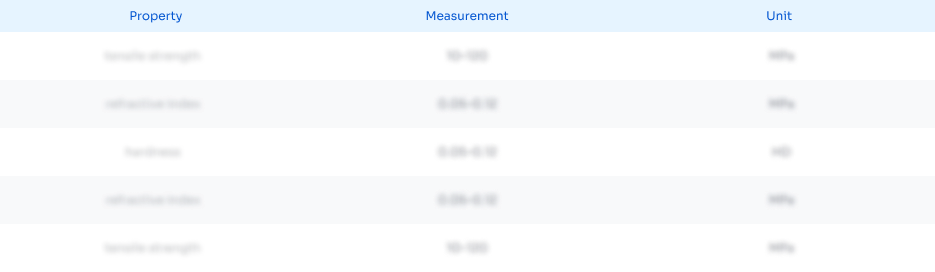
Abstract
Description
Claims
Application Information

- Generate Ideas
- Intellectual Property
- Life Sciences
- Materials
- Tech Scout
- Unparalleled Data Quality
- Higher Quality Content
- 60% Fewer Hallucinations
Browse by: Latest US Patents, China's latest patents, Technical Efficacy Thesaurus, Application Domain, Technology Topic, Popular Technical Reports.
© 2025 PatSnap. All rights reserved.Legal|Privacy policy|Modern Slavery Act Transparency Statement|Sitemap|About US| Contact US: help@patsnap.com