Method for manufacturing a mould element for a tyre mould
A technology for tire molds and molds, which can be applied to household appliances, other household appliances, tires, etc., and can solve problems such as aluminum patterns are not resistant to tire curing environments or mold cleaning operations
- Summary
- Abstract
- Description
- Claims
- Application Information
AI Technical Summary
Problems solved by technology
Method used
Image
Examples
Embodiment Construction
[0056] figure 1 Partly shown is an exemplary embodiment of a manufacturing apparatus, indicated generally at 10 , which is arranged for molding mold elements intended for tire curing moulds.
[0057] In the exemplary embodiment shown, the apparatus 10 is designed to be able to obtain, by moulding, mold elements which, when mounted in the associated curing molds, then allow the formation of a profile in the tread of the tyre. This is called an insert element.
[0058] Apparatus 10 includes a die 12 and an opposing die 14 each secured to two locations of the tool (not shown) and capable of being displaced along an axis of displacement between an open distanced position and a closed molding position. XX' move relative to each other. In the closed position of the device 10, the mold 12 and the opposing mold 14 bear against each other and define between them a molding cavity 16 of the mold element.
[0059] The molding cavity 16 defines in a concave manner the general shape of t...
PUM
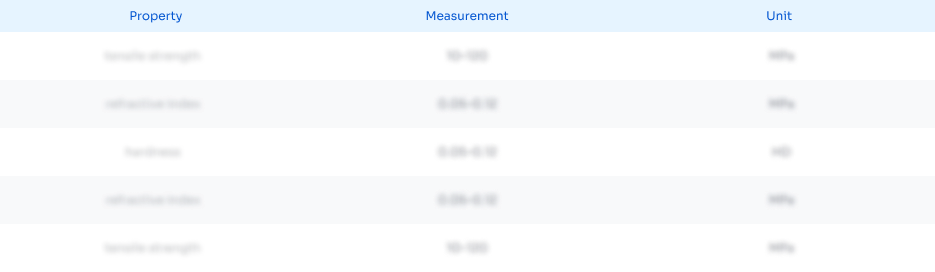
Abstract
Description
Claims
Application Information

- Generate Ideas
- Intellectual Property
- Life Sciences
- Materials
- Tech Scout
- Unparalleled Data Quality
- Higher Quality Content
- 60% Fewer Hallucinations
Browse by: Latest US Patents, China's latest patents, Technical Efficacy Thesaurus, Application Domain, Technology Topic, Popular Technical Reports.
© 2025 PatSnap. All rights reserved.Legal|Privacy policy|Modern Slavery Act Transparency Statement|Sitemap|About US| Contact US: help@patsnap.com