Inner chamfer machining robot for cylindrical parts
A robot and chamfering technology, applied in metal processing machinery parts, metal processing, metal processing equipment, etc., can solve problems such as poor processing accuracy, poor quality, and low efficiency
- Summary
- Abstract
- Description
- Claims
- Application Information
AI Technical Summary
Problems solved by technology
Method used
Image
Examples
Embodiment Construction
[0054] The following description serves to disclose the present invention to enable those skilled in the art to carry out the present invention. The preferred embodiments described below are only examples, and those skilled in the art can devise other obvious variations.
[0055] Such as figure 1Said, the cylindrical part includes a first cylinder 101 and a second cylinder 102, the first cylinder 101 and the second cylinder 102 are coaxially arranged, and one end of the second cylinder 102 is connected to the first cylinder 101 is connected at one end, and the outer diameter of the second cylindrical body 102 is larger than that of the first cylindrical body 101 .
[0056] refer to Figure 2-11 As shown, a processing robot for internal chamfering of cylindrical parts includes a horizontally placed mounting plate 1, a rotating disk 1b that is rotatable along the vertical axis and located directly above the mounting plate 1, and a loading station The feeding assembly 2 for lo...
PUM
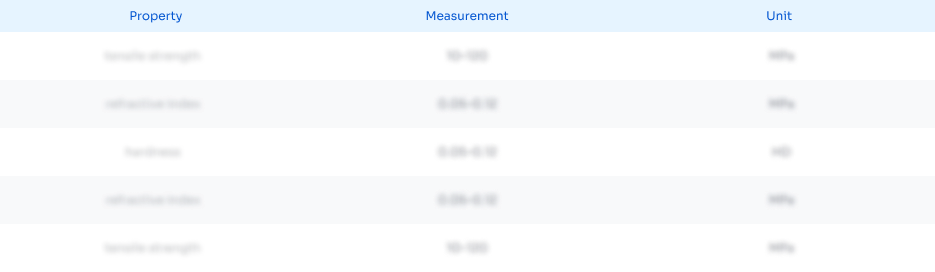
Abstract
Description
Claims
Application Information

- R&D Engineer
- R&D Manager
- IP Professional
- Industry Leading Data Capabilities
- Powerful AI technology
- Patent DNA Extraction
Browse by: Latest US Patents, China's latest patents, Technical Efficacy Thesaurus, Application Domain, Technology Topic, Popular Technical Reports.
© 2024 PatSnap. All rights reserved.Legal|Privacy policy|Modern Slavery Act Transparency Statement|Sitemap|About US| Contact US: help@patsnap.com