Automatic networking equipment and steel mesh cage processing system
An automatic networking and equipment technology, applied to wire processing, metal processing equipment, wire netting, etc., can solve the problems of lower networking efficiency, low efficiency, and lower production efficiency of autoclaved aerated concrete slabs, so as to improve connection efficiency , The effect of improving assembly efficiency
- Summary
- Abstract
- Description
- Claims
- Application Information
AI Technical Summary
Problems solved by technology
Method used
Image
Examples
Embodiment 1
[0049] like figure 1 and figure 2 As shown, an embodiment of the present invention provides an automatic networking device. The automatic networking equipment includes a workpiece support 30 , a workpiece mounting mechanism 100 , a networking mechanism 200 , a mesh lifting mechanism 50 and a first cantilever structure 40 . Wherein, the workpiece support 30 has a storage space for storing a plurality of steel rods; the workpiece mounting mechanism 100 includes a snap support device 70 with a plurality of mounting holes 713, and at least part of the workpiece mounting mechanism 100 is vertically movable up and down. Driven by at least part of the workpiece mounting mechanism 100 , the buckle supporting device 70 and the buckle 2 located in each installation hole 713 can move to a preset position corresponding to the steel drill 31 in the vertical direction, so as to install the buckle 2 on the Steel drill 31; the networking mechanism 200 includes a mesh support structure 20 f...
Embodiment 2
[0145] Different from the first example, as Figure 10As shown, in the second embodiment of the present invention, the first cantilever structure 40 includes two first cantilever portions 42 with a predetermined distance. Likewise, the second cantilever structure 45 includes two second cantilever parts 46 with a preset distance. The second cantilever parts 46 are used to support the first cantilever part 42 and prevent the first cantilever part 42 from being deformed to ensure better The longitudinal ribs that support the mesh.
[0146] It should be noted that the setting of the preset distance needs to ensure that the two first cantilever portions 42 can simultaneously support the outermost longitudinal ribs of the mesh sheet (ie, the uppermost longitudinal ribs and the lowermost longitudinal ribs). For example, the preset distance can be set to be equal to the vertical distance between the outermost longitudinal ribs of the mesh sheet, so that by lifting the entire first ca...
Embodiment 3
[0149] Different from the first example, as Figure 11 As shown, the networking mechanism 200 includes two first cantilever structures 40 and two second cantilever structures 45 corresponding to the two first cantilever structures 40 . The uppermost longitudinal rib and the lowermost longitudinal rib of the sheet are supported.
[0150] In this way, two second driving structures 55 also need to be provided, so that the two first cantilever structures 40 can be driven away from each other, so as to simultaneously clip the mesh into the upper buckle and the lower buckle. Automate the networking process.
[0151] Other structures in the third embodiment are the same as those in the first embodiment, and are not repeated here.
PUM
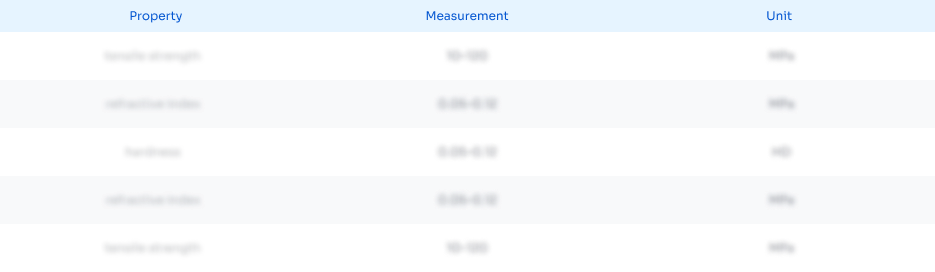
Abstract
Description
Claims
Application Information

- R&D
- Intellectual Property
- Life Sciences
- Materials
- Tech Scout
- Unparalleled Data Quality
- Higher Quality Content
- 60% Fewer Hallucinations
Browse by: Latest US Patents, China's latest patents, Technical Efficacy Thesaurus, Application Domain, Technology Topic, Popular Technical Reports.
© 2025 PatSnap. All rights reserved.Legal|Privacy policy|Modern Slavery Act Transparency Statement|Sitemap|About US| Contact US: help@patsnap.com