Preparation method of wear-resistant SBS sole material
A shoe sole material and wear-resistant technology, applied in shoe soles, footwear, applications, etc., can solve problems such as poor wear resistance, achieve the effects of reducing wear, improving strength and wear resistance, and reducing energy consumption
- Summary
- Abstract
- Description
- Claims
- Application Information
AI Technical Summary
Problems solved by technology
Method used
Image
Examples
Embodiment I
[0033] (1) Nano-SiO 2 Add to the mixed solution of ethanol and water, high-speed shear to disperse, then reduce the speed, add nano-SiO 2 10% Si75 silane coupling agent by mass and 0.1% catalyst dibutyltin dilaurate to adjust the pH value to 5. After reacting for 90 minutes, filter and dry the filter cake to obtain modified nano-SiO 2 I.
[0034] (2) A small amount of SBS and 5 parts of modified nano-SiO 2 1, 5 parts of white oil, 0.5 part of antioxidant tris (2,4-di-tert-butylphenyl) phosphite are banburyed and mixed in a banbury mixer to obtain pretreatment masterbatch I, then remaining SBS, 1 part The anti-aging agent N-isopropyl-N'-phenyl-p-phenylenediamine and the pretreatment masterbatch I are mixed and granulated in a twin-screw extruder to obtain the wear-resistant SBS shoe sole material I.
[0035] Example II
[0036] (1) Nano-SiO 2 Add to the mixed solution of ethanol and water, high-speed shear to disperse, then reduce the speed, add nano-SiO 2 15% by mass of...
Embodiment
[0039] (1) Nano-SiO 2 Add to the mixed solution of ethanol and water, high-speed shear to disperse, then reduce the speed, add nano-SiO 2 20% KH-570 silane coupling agent and 0.15% catalyst tetraethylenepentamine, adjust the pH value to 3, react for 240min, filter, and dry the filter cake to obtain modified nano-SiO 2 Ⅲ.
[0040] (2) A small amount of SBS and 1 part of modified nano-SiO 2 Ⅲ, 8 parts of white oil, 1 part of antioxidant 4-[(4,6-dioctylthio-1,3,5-triazin-2-yl)amino]-2,6-bis(1,1 -Methyl ethyl) phenol is mixed in the internal mixer to get the pretreatment masterbatch III, and then the remaining SBS S, 3 parts of anti-aging agent 2,2,4-trimethyl-1,2-dihydroquinoline 1. The pretreatment masterbatch III is mixed in a twin-screw extruder, extruded and granulated to obtain the wear-resistant SBS shoe sole material III.
[0041] (4) Embodiment IV
[0042] An X-ray photoelectron spectrometer, model: ESCALab-250Xi, is used for testing at an experimental temperature of...
PUM
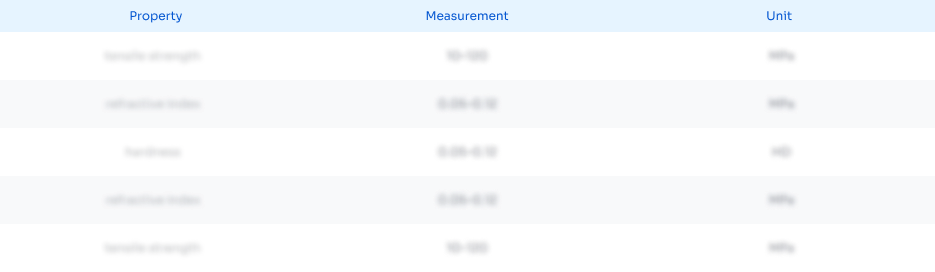
Abstract
Description
Claims
Application Information

- Generate Ideas
- Intellectual Property
- Life Sciences
- Materials
- Tech Scout
- Unparalleled Data Quality
- Higher Quality Content
- 60% Fewer Hallucinations
Browse by: Latest US Patents, China's latest patents, Technical Efficacy Thesaurus, Application Domain, Technology Topic, Popular Technical Reports.
© 2025 PatSnap. All rights reserved.Legal|Privacy policy|Modern Slavery Act Transparency Statement|Sitemap|About US| Contact US: help@patsnap.com