Comprehensive recovery treatment process of aniline tar
A kind of technology for recovery and treatment of aniline tar, which is applied in tar processing, tar processing through chemical method, petroleum industry, etc. It can solve problems such as economic loss, air and environmental pollution, and unutilized resources.
- Summary
- Abstract
- Description
- Claims
- Application Information
AI Technical Summary
Problems solved by technology
Method used
Image
Examples
Embodiment 1
[0036] like figure 1 In the process flow diagram shown, acetic acid and toluene are used to configure the organic solvent according to the mass ratio of 1:500, and a rectification tower with a theoretical plate number of 62 is used to mix the organic solvent and aniline tar according to the mass ratio of 50:1 Mix, and enter the rectification tower from the 7th tray, and pass into hydrogen below the 62 trays of the rectification tower, and control the hydrogen feed rate to be 10wt% of the tar feed amount; A stream of water is fed into each tray, and the mass ratio of water and tar is controlled to be 1:2; The upper section of the rectification tower realizes the hydrocracking of heavy components such as tar, and the organic solvent-containing material is obtained at the top of the rectification tower; the lower section of the rectification tower realizes the hydrogenation of tar cracking products, and the The catalyst and cracked hydrogenation products are discharged from the ...
Embodiment 2
[0041] The recovery and treatment process of aniline tar described in this embodiment is the same as that of Example 1, the only difference being that the mass ratio of the organic solvent to the tar is controlled to be 70:1, wherein the organic solvent is formic acid and toluene according to the mass ratio 1:700 is configured, and the temperature of the distillation tower is controlled at 242°C, the reflux ratio is 2.5, and the other parameters and rectification parameters remain unchanged.
[0042] After the operation of the rectification tower is stable, the light component product containing the organic solvent discharged from the top of the tower is collected, and after it is separated into two phases, the separated water phase is returned to the rectification tower for replenishing water.
[0043] After the distillation tower device is running stably, the components discharged from the tower kettle are collected and separated by suction filtration to obtain solid precious...
Embodiment 3
[0046] The recovery and treatment process of aniline tar described in this embodiment is the same as in Example 1, the only difference being that a rectifying tower with 75 theoretical plates is used, and the mixture of organic solvent and tar is controlled from the 7th plate. Enter the rectification tower, pass hydrogen gas under the 75 trays of the rectification tower, pass a stream of water at the 42nd tray of the rectification tower, control the temperature of the tower kettle at 240 ° C, the reflux ratio of 2, and other parameters and rectification The parameters are unchanged.
[0047] After the operation of the rectification tower is stable, the light component product containing the organic solvent discharged from the top of the tower is collected, and after it is separated into two phases, the separated water phase is returned to the rectification tower for replenishing water.
[0048] After the device is running stably, the components discharged from the tower kettle...
PUM
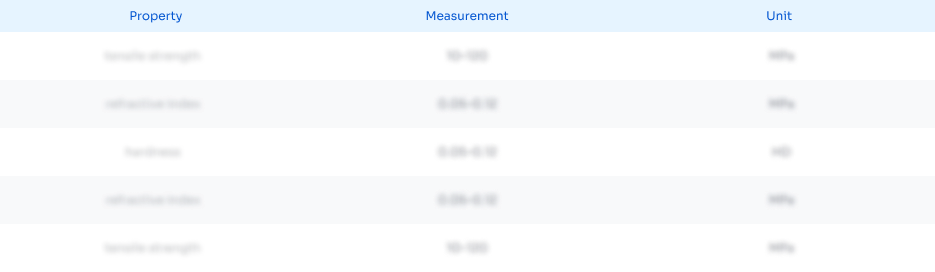
Abstract
Description
Claims
Application Information

- Generate Ideas
- Intellectual Property
- Life Sciences
- Materials
- Tech Scout
- Unparalleled Data Quality
- Higher Quality Content
- 60% Fewer Hallucinations
Browse by: Latest US Patents, China's latest patents, Technical Efficacy Thesaurus, Application Domain, Technology Topic, Popular Technical Reports.
© 2025 PatSnap. All rights reserved.Legal|Privacy policy|Modern Slavery Act Transparency Statement|Sitemap|About US| Contact US: help@patsnap.com