Clean steel smelting system and method
A smelting method and technology for cleaning steel, applied in the field of metallurgy, can solve the problems of complex design of load-bearing structures, increased natural temperature drop of molten steel, and reduced yield of alloys, so as to suppress the formation of oxide inclusions, reduce load-bearing requirements, and reduce refining The effect of cycle sum
- Summary
- Abstract
- Description
- Claims
- Application Information
AI Technical Summary
Problems solved by technology
Method used
Image
Examples
Embodiment
[0045] A clean steel smelting system, comprising a primary smelting furnace 1, a first diversion tank 2, a slag-steel separation device 3, a second diversion tank 4, a refining furnace 5, a continuous casting ladle 6 and a slag tank 7, wherein the refining furnace 5 Adopt induction heating vacuum refining furnace.
[0046] The first diversion tank 2 is connected to the primary smelting furnace 1 and the slag-steel separating device 3 , one end of which is located below the tapping hole 10 of the primary smelting furnace, and the other end is located above the slag-steel separating device 3 .
[0047] The second diversion groove 4 is connected to the slag-steel separation device 3 and the refining furnace 5 , one end of which is located below the tap hole 8 of the slag-steel separation device, and the other end is located above the refining furnace 5 .
[0048] When the primary smelting furnace 1 finishes smelting, the molten steel flows out from the tapping hole 10 of the prim...
PUM
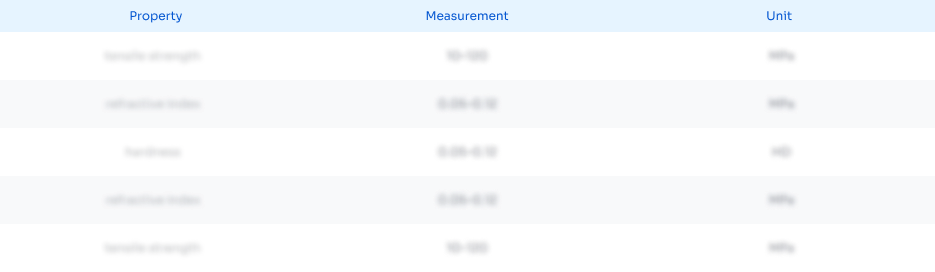
Abstract
Description
Claims
Application Information

- R&D Engineer
- R&D Manager
- IP Professional
- Industry Leading Data Capabilities
- Powerful AI technology
- Patent DNA Extraction
Browse by: Latest US Patents, China's latest patents, Technical Efficacy Thesaurus, Application Domain, Technology Topic, Popular Technical Reports.
© 2024 PatSnap. All rights reserved.Legal|Privacy policy|Modern Slavery Act Transparency Statement|Sitemap|About US| Contact US: help@patsnap.com