Machine tool large part structure optimization method considering gravity and heat influence
An optimization method and technology of thermal influence, applied in design optimization/simulation, computer-aided design, special data processing applications, etc., can solve the problems of large deformation of machine tools, low machining accuracy, and high manufacturing costs, to improve heat dissipation performance, increase Convective heat transfer coefficient, the effect of improving component stiffness
- Summary
- Abstract
- Description
- Claims
- Application Information
AI Technical Summary
Problems solved by technology
Method used
Image
Examples
Embodiment Construction
[0115] The present invention will be described in detail below in conjunction with the accompanying drawings.
[0116] A method for optimizing the structure of a large machine tool under the influence of gravity and heat of the present invention comprises the following steps:
[0117] Step 1. Define and calculate the heat source and heat dissipation boundary of the machine tool;
[0118] Step 2. Use ANSYS finite element software to simulate the deformation of large machine tool parts under the influence of gravity and heat;
[0119] Step 3. According to the finite element simulation results, optimize the structure of large parts with large deformation in the machine tool, such as drilling holes on the side and back of the bed and column, adding ribs, changing the arrangement of ribs, etc.;
[0120] Step 4. Carry out finite element simulation calculation on the deformation of the large machine tool after structural optimization, and verify the correctness and effectiveness of ...
PUM
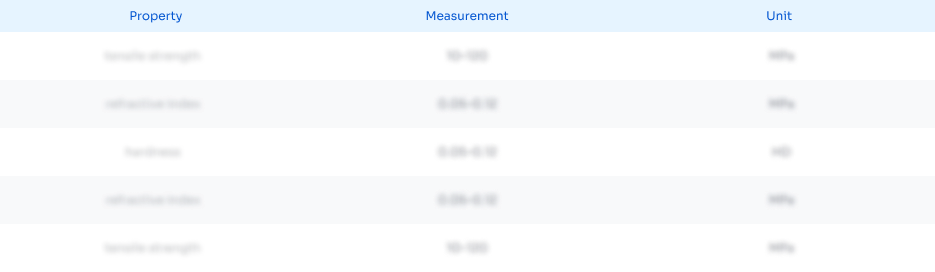
Abstract
Description
Claims
Application Information

- Generate Ideas
- Intellectual Property
- Life Sciences
- Materials
- Tech Scout
- Unparalleled Data Quality
- Higher Quality Content
- 60% Fewer Hallucinations
Browse by: Latest US Patents, China's latest patents, Technical Efficacy Thesaurus, Application Domain, Technology Topic, Popular Technical Reports.
© 2025 PatSnap. All rights reserved.Legal|Privacy policy|Modern Slavery Act Transparency Statement|Sitemap|About US| Contact US: help@patsnap.com