Measurement system and method with rolling angle self-correction function
A measurement system and roll angle technology, applied in measurement devices, instruments, optical devices, etc., can solve the problems of complex optical path, difficult to guarantee accuracy, difficult application, etc., and achieve the effect of simple optical path structure, improved measurement accuracy, and easy integration.
- Summary
- Abstract
- Description
- Claims
- Application Information
AI Technical Summary
Problems solved by technology
Method used
Image
Examples
Embodiment Construction
[0034] In order to facilitate those of ordinary skill in the art to understand and implement the present invention, the present invention will be further described in detail below in conjunction with the accompanying drawings and examples.
[0035] as attached figure 2As shown, the technical solution adopted in the present invention is: a five-degree-of-freedom error measurement system with the function of monitoring the non-parallelism of the double beams, the measurement system includes a semiconductor laser 1, a first beam splitter 2, a right-angle mirror 3, The second dichroic prism 4, the first four-quadrant photodetector 5, the first focusing lens 6, the second four-quadrant photodetector 7, the third dichroic prism 8, the third four-quadrant photodetector 9, the second focusing lens 10 , the fourth four-quadrant photodetector 11, the laser ranging module 12; wherein, the semiconductor laser 1, the first beam splitting prism 2, and the right-angle reflector 3 are instal...
PUM
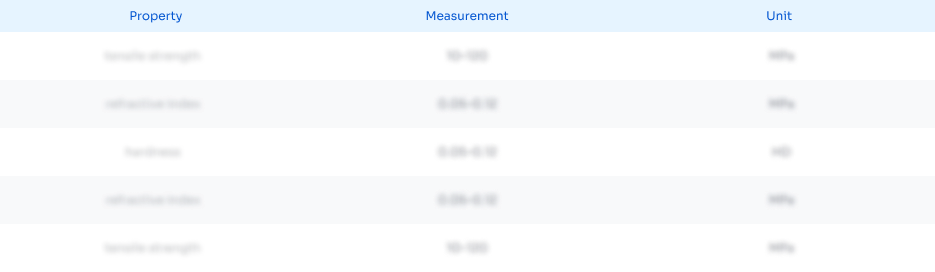
Abstract
Description
Claims
Application Information

- R&D
- Intellectual Property
- Life Sciences
- Materials
- Tech Scout
- Unparalleled Data Quality
- Higher Quality Content
- 60% Fewer Hallucinations
Browse by: Latest US Patents, China's latest patents, Technical Efficacy Thesaurus, Application Domain, Technology Topic, Popular Technical Reports.
© 2025 PatSnap. All rights reserved.Legal|Privacy policy|Modern Slavery Act Transparency Statement|Sitemap|About US| Contact US: help@patsnap.com