Light-weight aluminum alloy die casting surface treatment method
A surface treatment and die-casting technology, which is applied in the field of surface treatment of lightweight aluminum alloy die-castings, can solve the problems of reduced corrosion resistance of aluminum alloy die-castings, damage to the surface quality of die-castings, and easy generation of pores and sand holes
- Summary
- Abstract
- Description
- Claims
- Application Information
AI Technical Summary
Problems solved by technology
Method used
Image
Examples
Embodiment 1
[0046] see Figure 1-2 , a method for surface treatment of lightweight aluminum alloy die castings, comprising the following steps:
[0047] S1. Wash the surface of the aluminum alloy die casting with water to remove the dust and powder remaining on the surface of the aluminum alloy die casting during the production process. After washing, deburr and polish the surface of the aluminum alloy die casting;
[0048] S2. Perform shot blasting treatment on the die-casting aluminum alloy to remove the oxide skin on the surface of the die-casting part. After the shot blasting is completed, perform ultrasonic cleaning on it with ultrasonic equipment;
[0049] S3. Soak the aluminum alloy die casting in alkaline solution, then clean it with deionized water, and perform sandblasting after the end;
[0050] S4. Electroplating a layer of coating film on the surface of the aluminum alloy die casting, and then coating a layer of preservative mixed with magnetic materials on the coating film,...
Embodiment 2
[0062] A method for surface treatment of lightweight aluminum alloy die castings, comprising the following steps:
[0063] S1. Wash the surface of the aluminum alloy die casting with water to remove the dust and powder remaining on the surface of the aluminum alloy die casting during the production process. After washing, deburr and polish the surface of the aluminum alloy die casting;
[0064] S2. Perform shot blasting treatment on the die-casting aluminum alloy to remove the oxide skin on the surface of the die-casting part. After the shot blasting is completed, perform ultrasonic cleaning on it with ultrasonic equipment;
[0065] S3. Soak the aluminum alloy die casting in alkaline solution, then clean it with deionized water, and perform sandblasting after the end;
[0066] S4. Electroplating a layer of coating film on the surface of the aluminum alloy die casting, and then coating a layer of preservative mixed with magnetic materials on the coating film, and evenly embeddi...
Embodiment 3
[0073] A method for surface treatment of lightweight aluminum alloy die castings, comprising the following steps:
[0074] S1. Wash the surface of the aluminum alloy die casting with water to remove the dust and powder remaining on the surface of the aluminum alloy die casting during the production process. After washing, deburr and polish the surface of the aluminum alloy die casting;
[0075] S2. Perform shot blasting treatment on the die-casting aluminum alloy to remove the oxide skin on the surface of the die-casting part. After the shot blasting is completed, perform ultrasonic cleaning on it with ultrasonic equipment;
[0076] S3. Soak the aluminum alloy die casting in alkaline solution, then clean it with deionized water, and perform sandblasting after the end;
[0077] S4. Electroplating a layer of coating film on the surface of the aluminum alloy die casting, and then coating a layer of preservative mixed with magnetic materials on the coating film, and evenly embeddi...
PUM
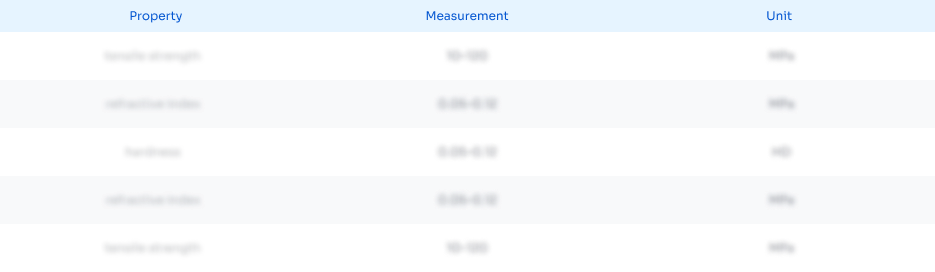
Abstract
Description
Claims
Application Information

- R&D Engineer
- R&D Manager
- IP Professional
- Industry Leading Data Capabilities
- Powerful AI technology
- Patent DNA Extraction
Browse by: Latest US Patents, China's latest patents, Technical Efficacy Thesaurus, Application Domain, Technology Topic, Popular Technical Reports.
© 2024 PatSnap. All rights reserved.Legal|Privacy policy|Modern Slavery Act Transparency Statement|Sitemap|About US| Contact US: help@patsnap.com