A kind of var smelting method for preparing full columnar crystal titanium alloy ingot
A titanium alloy and columnar crystal technology is applied in the field of VAR smelting for preparing full columnar crystal titanium alloy ingots, which can solve the problems of uneven structure in the edge and core of the bar and many forging times, and achieve the effect of solving the coarse solidification structure.
- Summary
- Abstract
- Description
- Claims
- Application Information
AI Technical Summary
Problems solved by technology
Method used
Image
Examples
Embodiment 1
[0018] Step 1: Put the secondary VAR melting Ti1023 alloy ingot with a weight of 1600kg and a specification of Φ440mm into a Φ520mm crucible, and place it in the melting station of the VAR furnace to seal the furnace and evacuate it. The water flow rate of the melting station is set to 1000L / min;
[0019] Step 2: When the pre-vacuum is ≤5Pa and the leakage rate is ≤1.0Pa / min, butt-weld the consumable electrode and the auxiliary electrode, and after cooling for 45 minutes, turn on the furnace to clean up the weld bumps, and then seal the furnace and evacuate after cleaning;
[0020] Step 3: When the pre-vacuum is ≤1Pa and the leakage rate is ≤0.6Pa / min, start arc melting. The melting voltage range is 28-30V, the melting current range is 10-14kA, and the arc-stabilizing current range is 5-10A AC. The arc stabilization period ranges from 6 to 10s.
[0021] Step 4: Start feeding when the remaining weight of the consumable electrode is 150kg. In the early stage of feeding, when th...
Embodiment 2
[0027] Step 1: Put the secondary VAR melting TC4 ingot with a weight of 5000kg and a specification of Φ640 into a Φ720mm crucible, and place it in the melting station of the VAR furnace to seal the furnace and evacuate it. Station water flow is set to 1200L / min;
[0028] Step 2: When the pre-vacuum is ≤5Pa and the leakage rate is ≤1.0Pa / min, butt-weld the consumable electrode and the auxiliary electrode, and after cooling for 45 minutes, turn on the furnace to clean up the weld bumps, and then seal the furnace and evacuate after cleaning;
[0029] Step 3: When the pre-vacuum is ≤1Pa and the leakage rate is ≤0.6Pa / min, start arc melting. The melting voltage range is 36-38V, the melting current range is 14-18kA, and the arc-stabilizing current range is 10-14A AC. The arc stabilization period ranges from 3 to 7s.
[0030] Step 4: Start feeding when the remaining weight of the consumable electrode is 350kg. In the early stage of feeding, when the current is greater than 8kA, the ...
Embodiment 3
[0037] Step 1: Put the secondary VAR melting Ti1023 ingot with a weight of 3500kg and a specification of Φ560mm into a Φ640mm crucible, and place it in the melting station of the VAR furnace to seal the furnace and evacuate it. Set the inlet water temperature of the melting station to 20°C and melt Station water flow is set to 1100L / min;
[0038] Step 2: When the pre-vacuum is ≤5Pa and the leakage rate is ≤1.0Pa / min, butt-weld the consumable electrode and the auxiliary electrode, and after cooling for 45 minutes, turn on the furnace to clean up the weld bumps, and then seal the furnace and evacuate after cleaning;
[0039] Step 3: When the pre-vacuum is ≤1Pa and the leakage rate is ≤0.6Pa / min, start arc melting, where the melting voltage range is 28-30V, the melting current range is 8-12kA, and the arc-stabilizing current range is 8-13A AC. The arc stabilization period ranges from 3 to 7s.
[0040] Step 4: Start feeding when the remaining weight of the consumable electrode is...
PUM
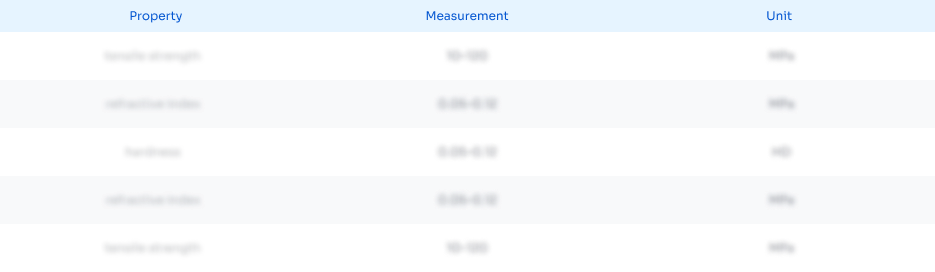
Abstract
Description
Claims
Application Information

- R&D
- Intellectual Property
- Life Sciences
- Materials
- Tech Scout
- Unparalleled Data Quality
- Higher Quality Content
- 60% Fewer Hallucinations
Browse by: Latest US Patents, China's latest patents, Technical Efficacy Thesaurus, Application Domain, Technology Topic, Popular Technical Reports.
© 2025 PatSnap. All rights reserved.Legal|Privacy policy|Modern Slavery Act Transparency Statement|Sitemap|About US| Contact US: help@patsnap.com