Processing technology of melt-blown non-woven fabric
A melt-blown non-woven fabric and processing technology, which is applied in the direction of non-woven fabrics, textiles and papermaking, and the melting of filament raw materials, can solve the problems of reducing heating effect, reducing shift effect, and uneven heating, etc. Improve the effect, improve the processing effect, improve the effect of stable shape
- Summary
- Abstract
- Description
- Claims
- Application Information
AI Technical Summary
Problems solved by technology
Method used
Image
Examples
Embodiment 1
[0032] Such as Figure 1-11 Shown, a kind of processing technology of meltblown nonwoven fabric, 1. may further comprise the steps:
[0033] a. Grinding: first, put the selected polypropylene raw material into the crushing device for crushing treatment. After the polypropylene crushing is completed, put the raw material into the grinder for secondary grinding. The grinding time is 40 minutes. The fineness of the raw material after grinding The degree of chemical transformation is 90 mesh;
[0034] b. Stirring: Put the ground raw materials in a into the stirring device, heat to 25°C and add deionized water into the stirring device, then stir and mix the ground raw materials, and pour them into the mixer during the stirring process of the raw materials Heating the toughening agent and continuing to stir, the stirring time was 60 minutes;
[0035] c. Spinning treatment: inject the molten mixture prepared in b into the melt-blown processing machine for spinning;
[0036] d. Pro...
Embodiment 2
[0042] A kind of processing technology of melt-blown non-woven fabric, comprises the following steps:
[0043] a. Pulverization: firstly, put the selected polypropylene raw material into a pulverization device for pulverization. After the polypropylene pulverization is completed, put the raw material into a grinder for secondary grinding. The grinding time is 60 minutes. The fineness of the raw material after grinding The degree of chemicalization is 100 mesh;
[0044] b. Stirring: Put the ground raw materials in a into the stirring device, heat to 30°C and add deionized water into the stirring device, then stir and mix the ground raw materials, and pour them into the blender during the stirring process of the raw materials Heating the toughening agent and continuing to stir, the stirring time was 80 minutes;
[0045] c. Spinning treatment: inject the molten mixture prepared in b into the melt-blown processing machine for spinning;
[0046] d. Processing: Process the fiber f...
Embodiment 3
[0048] A kind of processing technology of melt-blown non-woven fabric, comprises the following steps:
[0049] a. Pulverization: firstly, put the selected polypropylene raw material into a pulverization device for pulverization. After the polypropylene pulverization is completed, put the raw material into a grinder for secondary grinding. The grinding time is 50 minutes. The fineness of the raw material after grinding The chemical degree is 95 mesh;
[0050] b. Stirring: Put the ground raw materials in a into the stirring device, heat to 27°C and add deionized water into the stirring device, then stir and mix the ground raw materials, and pour them into the mixer during the stirring process of the raw materials Heating the toughening agent and continuing to stir, the stirring time was 70 minutes;
[0051] c. Spinning treatment: inject the molten mixture prepared in b into the melt-blown processing machine for spinning;
[0052] d. Processing: Process the fiber filaments prep...
PUM
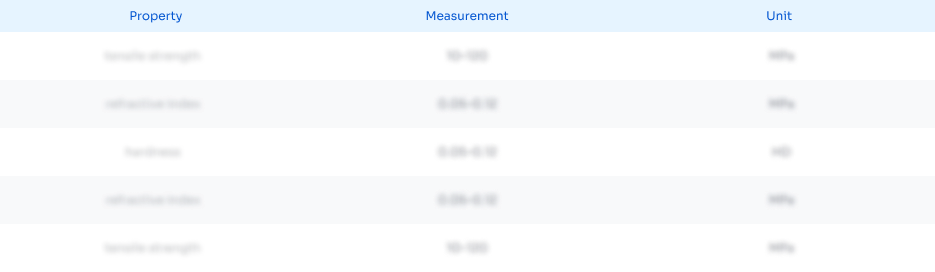
Abstract
Description
Claims
Application Information

- R&D Engineer
- R&D Manager
- IP Professional
- Industry Leading Data Capabilities
- Powerful AI technology
- Patent DNA Extraction
Browse by: Latest US Patents, China's latest patents, Technical Efficacy Thesaurus, Application Domain, Technology Topic, Popular Technical Reports.
© 2024 PatSnap. All rights reserved.Legal|Privacy policy|Modern Slavery Act Transparency Statement|Sitemap|About US| Contact US: help@patsnap.com