Preparation of tial by using Fe-containing waste aluminum alloy and waste SCR catalyst 3 Methods for Alloys and Low Fe Aluminum Alloys
A technology of SCR catalyst and waste aluminum alloy, which is applied in the field of resource utilization of solid waste to achieve the effect of low-cost, environment-friendly resource utilization
- Summary
- Abstract
- Description
- Claims
- Application Information
AI Technical Summary
Problems solved by technology
Method used
Image
Examples
Embodiment 1
[0022] Example 1: Preparation of TiAl using Fe-containing waste aluminum alloy and waste SCR catalyst 3 Alloys and methods for low Fe aluminium alloys (see figure 1 ),Specific steps are as follows:
[0023] (1) The waste SCR catalyst (TiO 2 The content is 75wt%, the main impurities and their content are 3.63wt% WO 3 , 1.20wt% V 2 O 5 , 4.32wt% SiO 2 , 1.32wt%CaO and 1.84wt%Al 2 O 3 ), Fe-containing scrap aluminum alloy (containing 1.75wt% Fe, 5.18wt% Si, 0.58wt% Mg, 1.27wt% Zn, 0.86wt% Mn and 1.50wt% Cu) and slag formers (CaO and Al 2 O 3 ) mixed uniformly, and then placed in an inert atmosphere (argon) and the temperature was 1873K for 180min reduction and smelting. After separation of slag and gold, Ti-Al alloy and waste slag containing 23.1wt% Ti were obtained; the waste SCR catalyst, Fe-containing Scrap aluminium alloys, CaO and Al 2 O 3 The mass ratio of 27:50:13:9;
[0024] (2) Place the Ti-Al alloy in step (1) in a resistance-heated directional solidificatio...
Embodiment 2
[0027] Example 2: Preparation of TiAl using Fe-containing waste aluminum alloy and waste SCR catalyst 3 Alloys and methods for low Fe aluminium alloys (see figure 1 ),Specific steps are as follows:
[0028] (1) The waste SCR catalyst (TiO 2 The content is 75wt%, the main impurities and their content are 3.63wt% WO 3 , 1.20wt% V 2 O 5 , 4.32wt% SiO 2 , 1.32wt%CaO and 1.84wt%Al 2 O 3 ), Fe-containing scrap aluminum alloy (containing 1.01wt% Fe, 2.41wt% Si, 0.89wt% Mg, 1.25wt% Zn, 0.52wt% Mn and 0.95wt% Cu) and slag formers (CaO and Al 2 O 3) mixed uniformly, and then placed in an inert atmosphere (argon) and the temperature was 1973K for 120min reduction and smelting, and after separation of the slag and gold, a Ti-Al alloy and waste slag containing 23.9wt% Ti were obtained; the waste SCR catalyst, Fe-containing Scrap aluminium alloys, CaO and Al 2 O 3 The mass ratio of 27:50:12:8;
[0029] (2) placing the Ti-Al alloy in step (1) in a directional solidification furna...
Embodiment 3
[0032] Example 3: Preparation of TiAl using Fe-containing waste aluminum alloy and waste SCR catalyst 3 Alloys and methods for low Fe aluminium alloys (see figure 1 ),Specific steps are as follows:
[0033] (1) The waste SCR catalyst (TiO 2 The content is 75wt%, the main impurities and their content are 3.63wt% WO 3 , 1.20wt% V 2 O 5 , 4.32wt% SiO 2 , 1.32wt%CaO and 1.84wt%Al 2 O 3 ), Fe-containing scrap aluminum alloy (containing 1.59wt% Fe, 1.51wt% Si, 0.82wt% Mg, 0.95wt% Zn, 0.31wt% Mn and 0.11wt% Cu) and slag-forming agent (CaO) were mixed uniformly, and then It was placed in an inert atmosphere (argon) and the temperature was 1873K for 60min reduction and smelting. After separation of slag and gold, Ti-Al alloy and waste slag containing 22.1wt% Ti were obtained; the waste SCR catalyst, Fe-containing waste aluminum alloy and CaO The mass ratio of 27:50:13;
[0034] (2) Place the Ti-Al alloy in step (1) in a directional solidification furnace heated by electromagne...
PUM
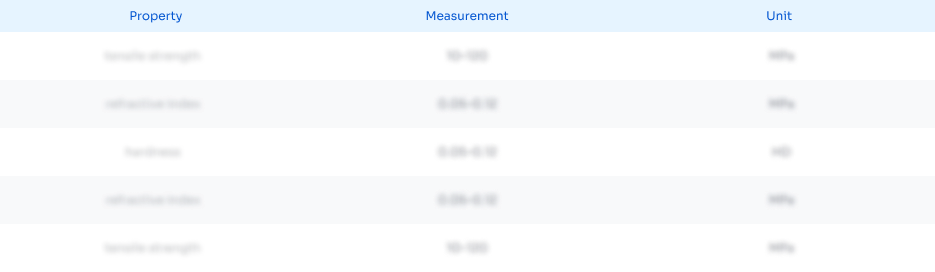
Abstract
Description
Claims
Application Information

- R&D
- Intellectual Property
- Life Sciences
- Materials
- Tech Scout
- Unparalleled Data Quality
- Higher Quality Content
- 60% Fewer Hallucinations
Browse by: Latest US Patents, China's latest patents, Technical Efficacy Thesaurus, Application Domain, Technology Topic, Popular Technical Reports.
© 2025 PatSnap. All rights reserved.Legal|Privacy policy|Modern Slavery Act Transparency Statement|Sitemap|About US| Contact US: help@patsnap.com