A six-axis industrial robot j2 joint and j3 joint stiffness measurement method
A technology of industrial robots and measurement methods, applied in manipulators, manufacturing tools, etc., can solve the problems of low accuracy, difficult operation, complicated calculation process, etc., and achieve the effect of low requirements, simple measurement equipment, and low cost
- Summary
- Abstract
- Description
- Claims
- Application Information
AI Technical Summary
Problems solved by technology
Method used
Image
Examples
Embodiment Construction
[0027] In order to make those skilled in the art better understand the technical solutions of the present invention, the present invention will be described more clearly and completely below with reference to the accompanying drawings in the embodiments. Of course, the described embodiments are only a part of the present invention. Not all, based on this embodiment, other embodiments obtained by those skilled in the art without creative labor are all within the protection scope of the present invention.
[0028] like Figure 1 to Figure 5 As shown, a method for measuring the stiffness of joints J2 and J3 of a six-axis industrial robot includes the following steps:
[0029] Step 1: Calculate the end load of the robot under test according to the parameters of the robot under test; take the J2 joint as an example, it is known that the model of the J2 joint reducer is 25-120, the maximum torque of the stiffness test is 87Nm, and the upper part of the arm can The maximum torque ap...
PUM
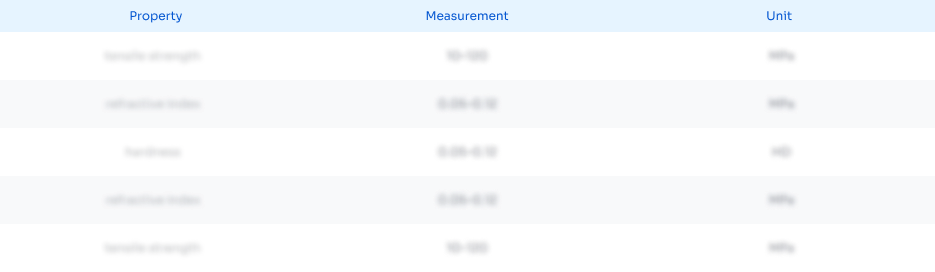
Abstract
Description
Claims
Application Information

- R&D
- Intellectual Property
- Life Sciences
- Materials
- Tech Scout
- Unparalleled Data Quality
- Higher Quality Content
- 60% Fewer Hallucinations
Browse by: Latest US Patents, China's latest patents, Technical Efficacy Thesaurus, Application Domain, Technology Topic, Popular Technical Reports.
© 2025 PatSnap. All rights reserved.Legal|Privacy policy|Modern Slavery Act Transparency Statement|Sitemap|About US| Contact US: help@patsnap.com