Thick copper backboard and manufacturing method thereof
A production method and backplane technology, which is applied in multilayer circuit manufacturing, printed circuit manufacturing, circuit lamination, etc., can solve the problems of high scrap rate, achieve high pass rate, simple production process, and fill the gaps in production
- Summary
- Abstract
- Description
- Claims
- Application Information
AI Technical Summary
Problems solved by technology
Method used
Image
Examples
Embodiment Construction
[0036] In order to make the object, technical solution and advantages of the present invention more clear, the present invention will be further described in detail below in conjunction with the examples. It should be understood that the specific embodiments described here are only used to explain the present invention, not to limit the present invention.
[0037] Aiming at the problems existing in the prior art, the present invention provides a method for manufacturing a thick copper backplane. The present invention will be described in detail below with reference to the accompanying drawings.
[0038] Such as figure 1 As shown, the thick copper backplane manufacturing method provided by the embodiment of the present invention includes the following steps:
[0039] S101, pre-etch the circuit out of a thick copper layer core board with an inner layer copper thickness greater than or equal to 105 μm;
[0040] S102. Laminating the thick copper layer core board first;
[0041]...
PUM
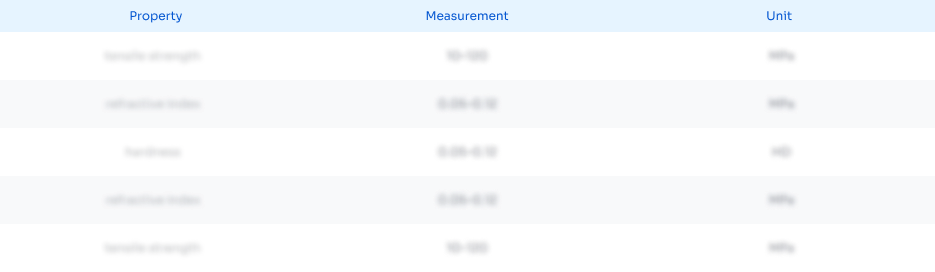
Abstract
Description
Claims
Application Information

- R&D Engineer
- R&D Manager
- IP Professional
- Industry Leading Data Capabilities
- Powerful AI technology
- Patent DNA Extraction
Browse by: Latest US Patents, China's latest patents, Technical Efficacy Thesaurus, Application Domain, Technology Topic, Popular Technical Reports.
© 2024 PatSnap. All rights reserved.Legal|Privacy policy|Modern Slavery Act Transparency Statement|Sitemap|About US| Contact US: help@patsnap.com