Transformer type force sensor
A force sensor and transformer-type technology, applied in the field of transformer-type force sensors, can solve the problems of not being able to fully meet the electro-hydraulic control requirements of high-horsepower tractors, and achieve the effect of reducing magnetic permeability and improving sensitivity
- Summary
- Abstract
- Description
- Claims
- Application Information
AI Technical Summary
Problems solved by technology
Method used
Image
Examples
Embodiment 1
[0024] This embodiment discloses a transformer type force sensor;
[0025] The transformer-type force sensor includes a force-bearing cylinder 1, and an excitation core 2 is installed in the force-bearing cylinder 1. The excitation core 2 includes an excitation pole 21, and an excitation coil 22 is wound around the periphery of the excitation pole 21. The number of turns and the connection method of the excitation coil 22 can be set according to actual needs, which is well known to those skilled in the art and will not be repeated here.
[0026] Two inductive magnetic cores 3 are installed symmetrically on both axial sides of the excitation magnetic core 2 in the bearing cylinder 1. The inductive magnetic cores 3 are two ferromagnets with the same size but different materials, which are respectively positive magnetostrictive Material ferromagnet and negative magnetostrictive material ferromagnet. Each induction core 3 includes an induction pole 31, and an induction coil 32 is...
Embodiment 2
[0033] In this embodiment, the excitation installation surface 23 is located on both sides of the excitation core 2 and the induction core 3 , there are two excitation installation surfaces 23 , and each excitation installation surface 23 is integrally formed. The top surface of the excitation installation surface 23 is in contact with the bearing cylinder 1 , and the height of the top surface of the excitation installation surface 23 corresponding to the excitation core 2 is lower than the top surface height of the excitation installation surface 23 corresponding to the induction core 3 . The space between the exciting magnetic core 2 and the two induction magnetic cores 3 is hollowed out.
Embodiment 3
[0035] The load-bearing cylinder 1 is processed from a circular tube. Of course, the load-bearing cylinder 1 can also be formed by drilling a pin shaft, and a step or slot structure 11 can be added on its outer peripheral surface for positioning and installation.
[0036] A positioning structure 11 is provided on the outer peripheral surface of the load-bearing cylinder 1, and the positioning structure 11 is a step or a slot for positioning and installation.
[0037] The load-bearing cylinder 1 is only used to carry and transmit external force, and it does not exist as a part of the magnetic circuit itself. The magnetic flux passing through the sleeve can be classified within the range of magnetic flux leakage. Therefore, the sleeve should adopt magnetic permeability It is made of materials with a low rate, or a magnetic isolation part is added in the contact area between the sleeve and the magnetic core to reduce the influence of magnetic flux leakage.
PUM
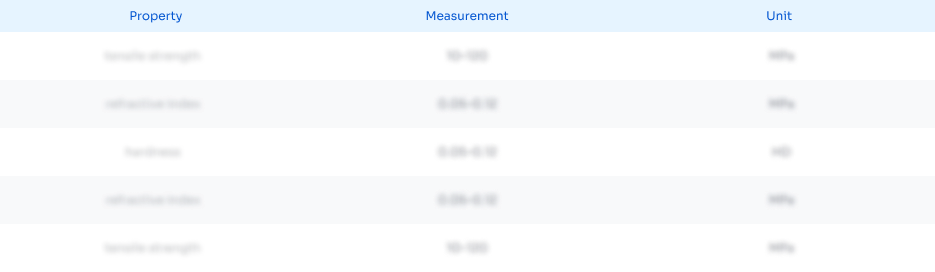
Abstract
Description
Claims
Application Information

- R&D Engineer
- R&D Manager
- IP Professional
- Industry Leading Data Capabilities
- Powerful AI technology
- Patent DNA Extraction
Browse by: Latest US Patents, China's latest patents, Technical Efficacy Thesaurus, Application Domain, Technology Topic, Popular Technical Reports.
© 2024 PatSnap. All rights reserved.Legal|Privacy policy|Modern Slavery Act Transparency Statement|Sitemap|About US| Contact US: help@patsnap.com