Self-assembly modular robot unit, robot and assembly and control method
A robotic and modular technology, applied in the direction of program control manipulators, manipulators, motor vehicles, etc., can solve the problems of few variable structures, weak automatic docking ability, lack of joint movement ability, etc., to increase structural diversity and success rate Improve and expand the effect of automatic docking movement range
- Summary
- Abstract
- Description
- Claims
- Application Information
AI Technical Summary
Problems solved by technology
Method used
Image
Examples
Embodiment Construction
[0065] In order to make the object, technical solution and advantages of the present invention clearer, the present invention will be further described in detail below in combination with specific embodiments and with reference to the accompanying drawings. It should be understood that these descriptions are exemplary only, and are not intended to limit the scope of the present invention. Also, in the following description, descriptions of well-known structures and techniques are omitted to avoid unnecessarily obscuring the concept of the present invention.
[0066] The purpose of the present invention is to provide a self-assembling modular robot unit and the group mobile self-assembling modular robot formed by it, so as to solve the problems in the prior art that the group robot forms less variable structures, weak automatic docking ability and poor connection after connection. Does not have problems such as joint movement ability.
[0067] The self-assembling modular robot...
PUM
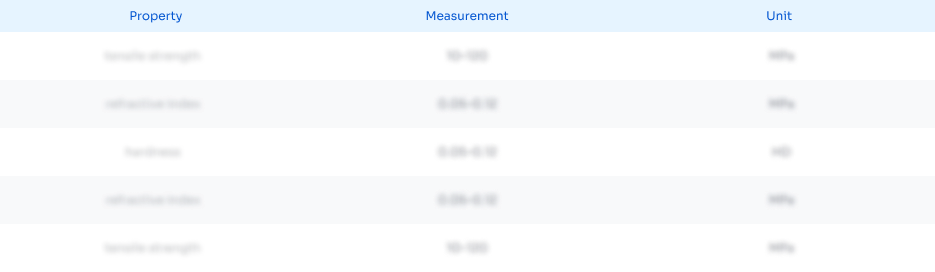
Abstract
Description
Claims
Application Information

- R&D Engineer
- R&D Manager
- IP Professional
- Industry Leading Data Capabilities
- Powerful AI technology
- Patent DNA Extraction
Browse by: Latest US Patents, China's latest patents, Technical Efficacy Thesaurus, Application Domain, Technology Topic, Popular Technical Reports.
© 2024 PatSnap. All rights reserved.Legal|Privacy policy|Modern Slavery Act Transparency Statement|Sitemap|About US| Contact US: help@patsnap.com