Simulation calibration method for mechanical properties of carbon fiber material
A carbon fiber material, calibration method technology, applied in the direction of analyzing materials, using stable shear force to test material strength, using stable tension/pressure to test material strength, etc., can solve the lack of system process and processing methods, control parameters It can shorten the development cycle, improve the calibration accuracy, and ensure the simulation accuracy.
- Summary
- Abstract
- Description
- Claims
- Application Information
AI Technical Summary
Problems solved by technology
Method used
Image
Examples
Embodiment Construction
[0038] Unless otherwise defined, the technical terms used in the following embodiments have the same meaning as commonly understood by those skilled in the art to which the present invention belongs. The test reagents used in the following examples, unless otherwise specified, are conventional biochemical reagents; the experimental methods, unless otherwise specified, are conventional methods.
[0039] The invention will be described in detail below in conjunction with the embodiments and accompanying drawings.
[0040] It should be noted that the type of calibration card selected in this example is the No. 58 material card in LS-DYNA. The carbon fiber process is WCM and RTM two process types, and the carbon fiber matrix is epoxy resin. The carbon fiber material mechanical performance simulation calibration method includes the following steps S1 to S7:
[0041] S1. Processing of carbon fiber unidirectional tape and typical laminate tensile, compressive, shearing, three-poi...
PUM
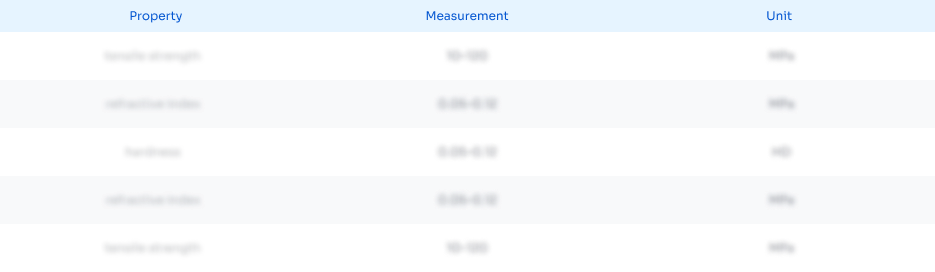
Abstract
Description
Claims
Application Information

- Generate Ideas
- Intellectual Property
- Life Sciences
- Materials
- Tech Scout
- Unparalleled Data Quality
- Higher Quality Content
- 60% Fewer Hallucinations
Browse by: Latest US Patents, China's latest patents, Technical Efficacy Thesaurus, Application Domain, Technology Topic, Popular Technical Reports.
© 2025 PatSnap. All rights reserved.Legal|Privacy policy|Modern Slavery Act Transparency Statement|Sitemap|About US| Contact US: help@patsnap.com