Rapid converter protection method for front large surface of converter
A fast, converter technology, applied in the field of metallurgy, can solve the problems of insufficient impact resistance, local furnace lining thinning, unfavorable dephosphorization, etc., to improve the safety of use, improve production efficiency, and reduce furnace repair costs.
- Summary
- Abstract
- Description
- Claims
- Application Information
AI Technical Summary
Problems solved by technology
Method used
Image
Examples
Embodiment 1
[0038] 1) At the end of converter blowing, the sub-lance TSO is used to determine the oxygen, and the oxygen activity is 500ppm.
[0039] 2) According to the oxygen activity of 500ppm, determine the coke consumption of 30kg. During the period from 1 minute of tapping to the end of tapping, the coke is put into the surface of the slag in the furnace. Composition mass percent of coke: 10% of ash, 4% of volatile matter, and 86% of fixed carbon. Particle size: ≤10mm.
[0040] 3) Confirm that the furnace area to be repaired is 4m 2 , 1.5t of magnesite and 1.0t of bar waste cutting head are loaded into the scrap steel bucket in advance. Magnesite Composition: Chemical Composition MgO: 42%, CO 2 : 48%, FeO: 7%, and the rest are impurities.
[0041] 4) After tapping, shake the furnace to 60 degrees, and quickly add the magnesite in the scrap bucket and the waste cutting head of the bar into the furnace. Then shake the furnace quickly to about 95 degrees and stay for 10 seconds, ...
Embodiment 2
[0048] 1) At the end of converter blowing, the sub-lance TSO is used to determine the oxygen, and the oxygen activity is 700ppm.
[0049] 2) According to the oxygen activity of 700ppm, determine the coke consumption of 40kg. During the period from 1 minute of tapping to the end of tapping, the coke is put into the surface of the slag in the furnace. Composition mass percent of coke: 8% ash, 6% volatile matter, 86% fixed carbon. Particle size: ≤10mm.
[0050] 3) Confirm that the furnace area to be repaired is 2m 2 , 1.0t of magnesite and 0.6t of bar waste cutting head are loaded into the scrap steel bucket in advance. Magnesite Composition: Chemical Composition MgO: 41%, CO 2 : 47%, FeO: 9%, and the rest are impurities.
[0051] 4) After tapping, shake the furnace to 60 degrees, and quickly add the magnesite in the scrap bucket and the waste cutting head of the bar into the furnace. Then quickly shake the furnace to about 95 degrees and stay for 10 seconds, finally shake ...
Embodiment 3
[0058] 1) At the end of converter blowing, the sub-lance TSO is used to determine the oxygen, and the oxygen activity is 900ppm.
[0059] 2) According to the oxygen activity of 900ppm, determine the consumption of 50kg of coke. During the period from 1 minute of tapping to the end of tapping, the coke is put into the surface of the slag in the furnace. Composition mass percent of coke: 12% ash, 1% volatile matter, 87% fixed carbon. Particle size: ≤10mm.
[0060] 3) Confirm that the furnace area to be repaired is 5m 2 , 1.5t of magnesite and 1.0t of bar waste cutting head are loaded into the scrap steel bucket in advance. Magnesite Composition: Chemical Composition MgO: 40%, CO 2 : 46%, FeO: 9%, and the rest are impurities.
[0061] 4) After tapping, shake the furnace to 60 degrees, and quickly add the magnesite in the scrap bucket and the waste cutting head of the bar into the furnace. Then shake the furnace quickly to about 95 degrees and stay for 10 seconds, finally sh...
PUM
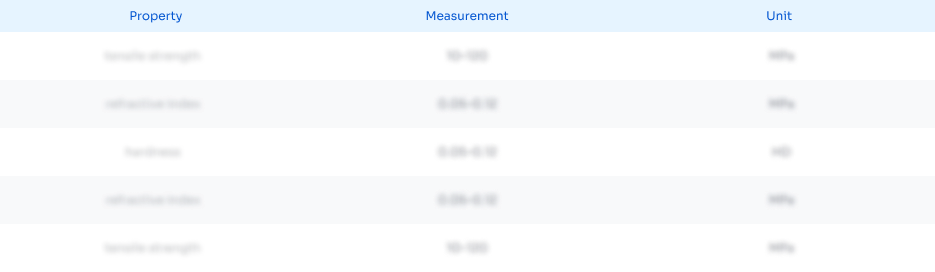
Abstract
Description
Claims
Application Information

- R&D
- Intellectual Property
- Life Sciences
- Materials
- Tech Scout
- Unparalleled Data Quality
- Higher Quality Content
- 60% Fewer Hallucinations
Browse by: Latest US Patents, China's latest patents, Technical Efficacy Thesaurus, Application Domain, Technology Topic, Popular Technical Reports.
© 2025 PatSnap. All rights reserved.Legal|Privacy policy|Modern Slavery Act Transparency Statement|Sitemap|About US| Contact US: help@patsnap.com