Carbon-free sintering method for providing heat by adopting high air temperature
A carbon sintering and heat technology, applied in the field of blast furnace ironmaking, can solve problems such as uncontrollable sintering process
- Summary
- Abstract
- Description
- Claims
- Application Information
AI Technical Summary
Problems solved by technology
Method used
Image
Examples
Embodiment 1
[0061] In this embodiment, a carbon-free sintering method that uses high wind temperature to provide heat, the specific steps are: weigh the raw materials in each sintering raw material bin 1 according to the set amount, discharge them on the feeding belt 2, and then put each The raw materials in the sintering raw material bin 1 are transferred to the cylindrical mixer 3 to form a mixture with a particle size of 10 mm, and then loaded into the mixing bin 4; then the bottom material is laid on the sintering trolley 5, and the bottom material adopts a particle size of 10mm, 20mm thick and fuel-free sintered ore, and then uniformly distributed along the height direction of the trolley, the thickness of the material layer is 800mm; Internal combustion forms high-temperature gas, and enters the high-temperature hot-air hood 7 and the low-temperature hot-air hood 6 through the pipeline, and controls the temperature of the high-temperature gas in the flue gas furnace 8 so that the tem...
Embodiment 2
[0063] A carbon-free sintering method using high wind temperature to provide heat in this embodiment, its specific steps are the same as in Example 1, the difference is that: the particle size of the mixture is 5mm; the bottom material used when laying the bottom material The particle size is 20mm, and the thickness is 40mm; the thickness of the material layer during the cloth is 700mm; the temperature of the hot air in the high-temperature hot-air cover 7 is 1300°C; the temperature of the hot-air in the low-temperature hot-air cover 6 is 800°C.
Embodiment 3
[0065] A carbon-free sintering method using high wind temperature to provide heat in this embodiment, its specific steps are the same as in Example 1, the difference is that: the particle size of the mixture is 8mm; the bottom material used when laying the bottom material The particle size is 15mm, and the thickness is 30mm; the thickness of the material layer is 750mm; the temperature of the hot air in the high temperature hot air cover 7 is 1330°C; the temperature of the hot air in the low temperature hot air cover 6 is 820°C.
PUM
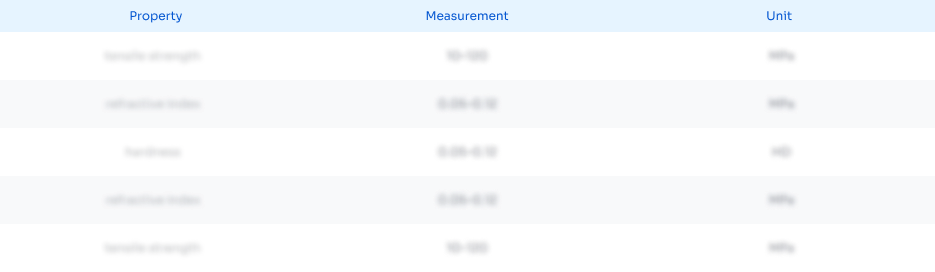
Abstract
Description
Claims
Application Information

- R&D Engineer
- R&D Manager
- IP Professional
- Industry Leading Data Capabilities
- Powerful AI technology
- Patent DNA Extraction
Browse by: Latest US Patents, China's latest patents, Technical Efficacy Thesaurus, Application Domain, Technology Topic, Popular Technical Reports.
© 2024 PatSnap. All rights reserved.Legal|Privacy policy|Modern Slavery Act Transparency Statement|Sitemap|About US| Contact US: help@patsnap.com