resistant to hcl-h 2 Corrosion, high temperature resistant coating and preparation method thereof
A high-temperature-resistant coating, hcl-h2s technology, applied in the direction of anti-corrosion coatings, polyurea/polyurethane coatings, polyester coatings, etc., can solve the problems of corrosiveness, industrial enterprise safety problems, economic losses, S corrosiveness, and high temperature resistance. and other problems, to achieve the effect of reducing dosage, improving self-crosslinking property, and good dispersion uniformity
- Summary
- Abstract
- Description
- Claims
- Application Information
AI Technical Summary
Problems solved by technology
Method used
Image
Examples
Embodiment 1
[0025] A resistant HCl-H 2 S corrosion and high temperature resistant coatings, raw materials include 6-amino-2-pyridine carboxylic acid, graphene oxide nanosheets, organic resin, polyethylene polyamine, trimethylolpropane trimethacrylate, diethylene glycol butyl ether, Organosiloxane resins, dispersants, anti-corrosion fillers, leveling agents, defoamers, water.
[0026] Firstly, the organic resin material functionalized with graphene ester of 6-amino-2-pyridinecarboxylate was prepared.
[0027] (1) Add 6-amino-2-pyridinecarboxylic acid and graphene nanosheets into the reactor according to the mass ratio of 10:2, use zinc isooctanoate as a catalyst, and react at 135°C for 12h to obtain 6-amino- Graphene 2-pyridinecarboxylate.
[0028] (2) Mix the organic resin and diethylene glycol butyl ether according to the mass ratio of 1:1, then heat up to 70°C, add polyethylene polyamine for heat preservation reaction for 1h, the molar ratio of polyethylene polyamine to organic resin ...
Embodiment 2
[0032]A resistant HCl-H 2 S corrosion and high temperature resistant coatings, raw materials include 6-amino-2-pyridine carboxylic acid, graphene oxide nanosheets, organic resin, polyethylene polyamine, trimethylolpropane trimethacrylate, diethylene glycol butyl ether, Organosiloxane resins, dispersants, anti-corrosion fillers, leveling agents, defoamers, water.
[0033] Firstly, the organic resin material functionalized with graphene ester of 6-amino-2-pyridinecarboxylate was prepared.
[0034] (1) Add 6-amino-2-pyridinecarboxylic acid and graphene oxide nanosheets into the reactor at a mass ratio of 10:3, use zinc isooctanoate as a catalyst, and react at 120°C for 13 hours to obtain 6-amino - Graphene 2-pyridinecarboxylate.
[0035] (2) Mix the organic resin and diethylene glycol butyl ether according to the mass ratio of 1:(1-2), then heat up to 80°C, add polyethylene polyamine for heat preservation reaction for 1h, polyethylene polyamine and organic The molar ratio of r...
Embodiment 3
[0040] A resistant HCl-H 2 S corrosion and high temperature resistant coatings, raw materials include 6-amino-2-pyridine carboxylic acid, graphene oxide nanosheets, organic resin, polyethylene polyamine, trimethylolpropane trimethacrylate, diethylene glycol butyl ether, Organosiloxane resins, dispersants, anti-corrosion fillers, leveling agents, defoamers, water.
[0041] Firstly, the organic resin material functionalized with graphene ester of 6-amino-2-pyridinecarboxylate was prepared.
[0042] (1) Add 6-amino-2-pyridinecarboxylic acid and graphene oxide nanosheets into the reactor at a mass ratio of 10:1, use zinc isooctanoate as a catalyst, and react at 145°C for 10 hours to obtain 6-amino - Graphene 2-pyridinecarboxylate.
[0043] (2) Mix the organic resin and diethylene glycol butyl ether according to the mass ratio of 1:2, then heat up to 75°C, add polyethylene polyamine for heat preservation reaction for 1h, the molar ratio of polyethylene polyamine to organic resin ...
PUM
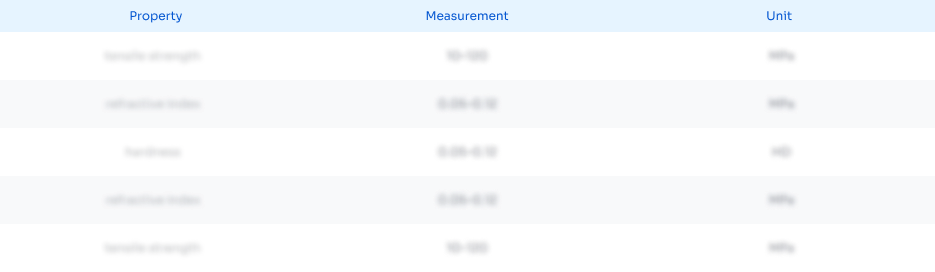
Abstract
Description
Claims
Application Information

- Generate Ideas
- Intellectual Property
- Life Sciences
- Materials
- Tech Scout
- Unparalleled Data Quality
- Higher Quality Content
- 60% Fewer Hallucinations
Browse by: Latest US Patents, China's latest patents, Technical Efficacy Thesaurus, Application Domain, Technology Topic, Popular Technical Reports.
© 2025 PatSnap. All rights reserved.Legal|Privacy policy|Modern Slavery Act Transparency Statement|Sitemap|About US| Contact US: help@patsnap.com